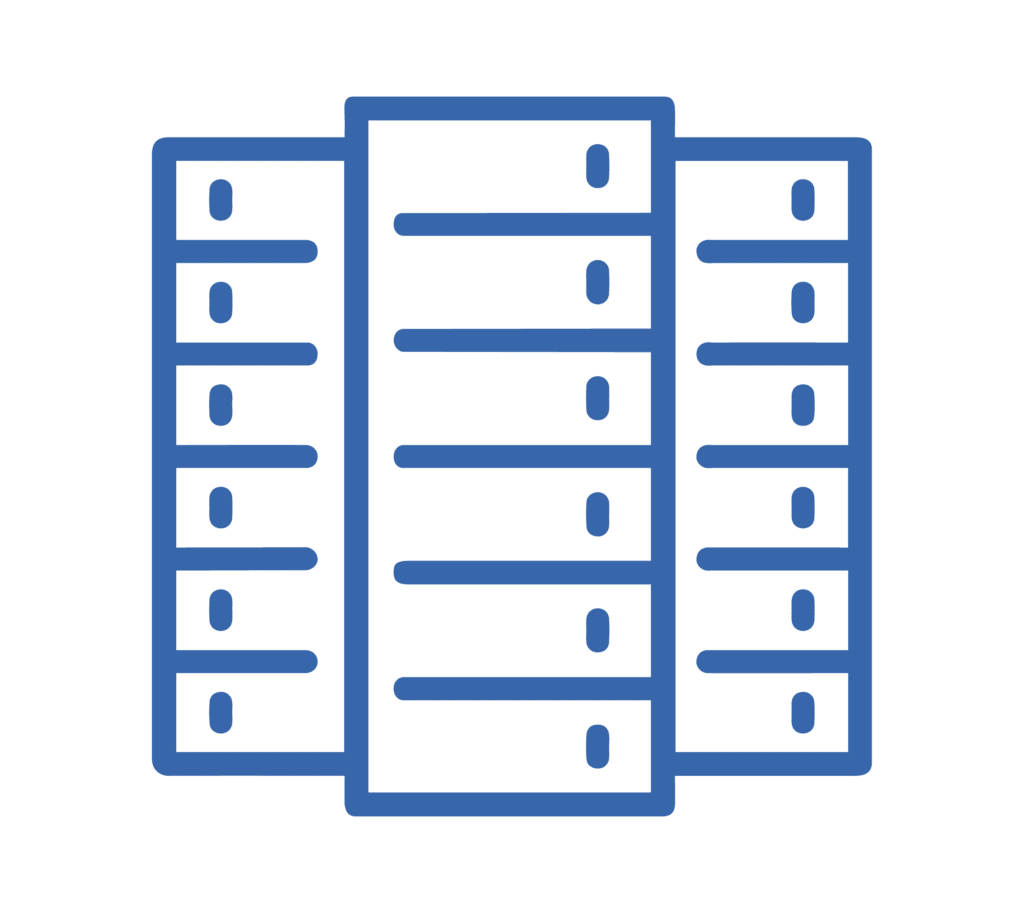
Integrating an Electrical Power Monitor System in Parallel with an Existing System
E Tech Group installed and commissioned a standard Electrical Power Monitoring System (EPMS) in parallel with a data center’s existing system to maintain the original combined EPMS and Building Management System (BMS) until it could be upgraded.
The Project: Install a New EPMS in Tandem with an Existing EPMS & BMS System
A social media platform Data Center needed their standard Electrical Power Monitor System (EPMS) installed and commissioned to work in parallel with their older existing system. The existing system was a combined EPMS and Building Management System (BMS) and needed to remain in place, as the BMS portion of the system wasn’t being replaced yet.
The multi-building Data Center campus and the SCADA system in some of the buildings is the current standard SCADA software, but in other buildings, older SCADA software was in place from a different vendor needing alignment.
The client wanted to eliminate device connections utilizing the BACnet/IP protocol and replace them with Modbus/TCP protocol to ensure current system standards are being met. As well, they wanted to standardize points being polled and monitored to match the current standards of the newer sites within the data center fleet.
E Tech Group’s reputation within the client’s organization, performance on a prior project, and because our feasibility study gave the client confidence that the project had a high level of probability that it could be accomplished within the limited timeframe allowed, we were selected to complete this project.
The Challenge: Keep Everyone Calm, Meet Harsh Deadlines, Exceed Client Expectations
E Tech Group’s automation team knew they needed to provide continuity to rectify the impact the client was currently experiencing as well as become familiar with and operate within two systems instead of just one. The aggressive timeline coupled with multiple moratorium periods to work around required an incredibly strategic and efficient approach.
The client was concerned that it wasn’t feasible to have an additional system polling for data in parallel and the equipment wouldn’t be able to support the additional requests. Some of the equipment was already being polled by 3-4 other systems monitoring the data. E Tech Group:
- Performed a feasibility study/risk assessment as an initial phase of this project.
- Evaluated each device type to determine limitations and assess which devices might experience bandwidth, connection limit, and response time issues.
- Developed a plan to mitigate the issues.
The BACnet/IP communication modules in the generator control panels needed to be replaced with Modbus/TCP communication modules. The design of the panels made it necessary to perform a Lock Out – Tag Out (LOTO) of each generator to install the new communication modules safely. We worked with site Operations and developed a schedule to perform the work, aligning as much as possible with their planned maintenance activities.
The Solution: Gain the Client Confidence Needed for Our Team to Divide & Conquer
The Feasibility Study mentioned earlier provided confidence in the proposed solution, and its approval was a catalyst for team members to move forward knowing they had a tight timeline they were up against.
To divide and conquer, E Tech Group subcontracted the SCADA developer required by the customer and managed the development of the EPMS SCADA application.
- PowerSCADA was the software platform used as the client’s standard.
- It was developed in phases in order to meet the project schedule, which required tracking changes with each version and verification to ensure the final application incorporated all of the necessary edits.
- Our team performed bench testing of each field equipment type using a Modbus simulation device to verify the graphic templates and tags were linked as expected.
- We developed a commissioning plan and corresponding method of procedures for bringing the new system online. To avoid impacts to the live system our team tested one device type at a time and monitored the health of the existing system, ensuring the two were able to function together without interruption or conflict.
- Onsite and remote commissioning of the SCADA system and the data center infrastructure management (DCIM) interface.
The Result: Active Partnerships Create the Most Effective Control Systems
By partnering with the client, as opposed to just fulfilling a role or requirement, E Tech Group helped the customer get closer to their long-term vision of the system. The new EPMS system follows the standards used at other sites within the data center fleet.
The findings of the feasibility study proved to be accurate, and the information gathered allowed the system to be successfully commissioned without any major impacts to the live system.
The client stated they were incredibly satisfied with the way the project was executed during the lessons learned meeting at project completion. This successful commissioning of the EPMS SCADA application allowed the client to be ready for the upcoming project of integrating the Building Management System.