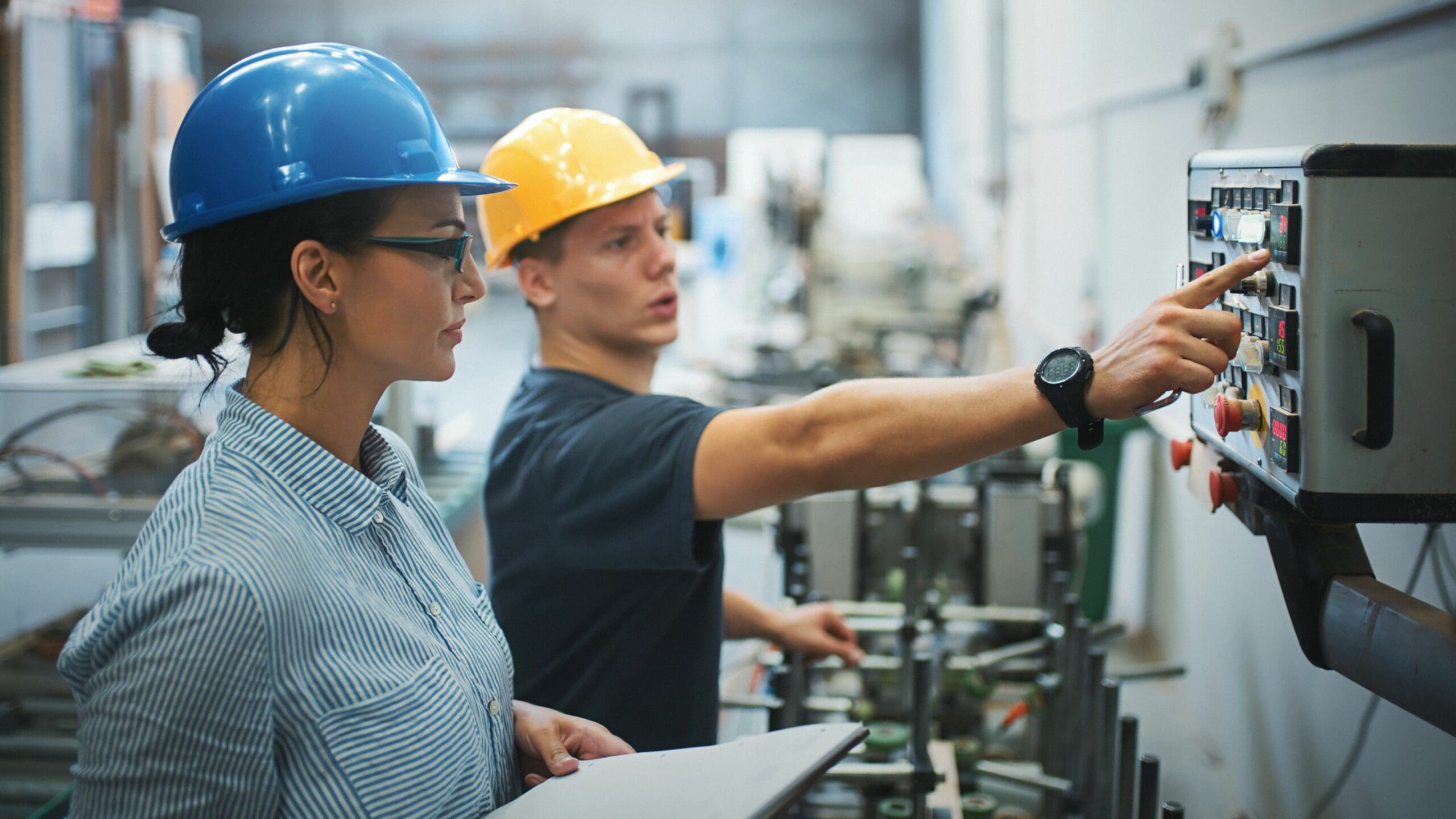
When it’s Time to Consider a Control Systems Upgrade: IT/OT Risk Assessment
When you’re working in a facility that has equipment reaching end of life or components that are on the verge of obsolescence, it would be nice to simply wave a wand and everything be instantly updated. Unfortunately, because multiple installations and upgrades have been done over a period of decades, this process tends to be a bit more involved. To better understand what’s wrong and what it will take to provide a fix, it really is imperative that the client is as involved in this process as are our engineers.
Because of the sheer number of issues and temporary band-aids placed on them, our clients often don’t know where to start. Compounded fixes over time make it difficult to identify the main issue or issues. That’s where we come in and can help add some rigor to this process. If we can have an open line of communication with the client’s decision makers and maintenance team, we can help them better understand what we’re assessing and what it will take to correct it. The goal is to take a large amount of material and truncate it into digestible pieces that will allow all parties to evaluate potential solutions.
Custom Automation Solutions Don’t Have to Start from Scratch
In many cases, maintenance technicians or employees may just think we’re there to redo the building. They see an engineer walking the floor and may assume they’re only there to complete a particular task, when in actuality we’re there to perform an in-depth assessment and present options to give them control over what optimizations are implemented.
Building automation and control systems integration is a specialized field; the client may not always aware of the extent of what could be, but are sometimes excited at the prospect of new equipment and connectivity; uplifting devices to Ethernet and a SCADA system that’s centralized.
Any reticence towards the upcoming automation changes shouldn’t be interpreted as opposition to change or an unwillingness to cooperate, it’s more a matter of not knowing what they should expect and simply being looped in at the end. But as we often see, projects cannot be fully-optimized without close collaboration between E Tech engineers and our client’s leadership.
With Facility Changes, it’s Important to Keep Everyone in the Loop
If read in from the beginning and actively engaged throughout the process, the engineer and employee could work in tandem to go around to all of the control panels, document all of their automation equipment, PLC, VFDs, switches, old drawings, control scheme network – anything that can give us a picture of how the current automation and controls work together (or don’t).
Our engineers would come back with that information to the office, assess it, and break it down for the client: Is it an end-of-life situation? Is there any obsolescence to deal with? What are the possibilities moving forward? This initial equipment and systems analysis is all to identify if there are any risk factors at play, and if an update is required.
We can also tell people what to prioritize – highlighting crucial equipment. One facility had a single, building-wide network. We redesigned their network topology to suite them better. Having walked the facility with our engineers, the employees and maintenance technicians now had the situational context to make a better-informed decision as it pertains to their facilities’ optimization.
We understand that this entire experience can seem daunting, but working closely with our engineers can make this process more digestible and really ensure you get what you need. To illustrate this synergistic relationship, let’s look at a specific case where E Tech Group helped assess a facility’s vulnerabilities and executed their optimization vision:
Case Study: Troubleshooting a Tangled Web of Out-of-Date Systems Integration
While working in a heavily-dated facility, it was discovered that all of their control panels were on one network, there were multiple manufacturers and versions of these devices, and they truly didn’t know what they had. Because it was such a tangled web, it took an entire day for the maintenance team to identify that it was one network switch that caused the whole facility to shut down.
Even though this was an Ethernet device, there was no centralized SCADA implemented to alarm in a control room and alert the maintenance team to the source of their downed lines. The downtime required just to identify the source of the control systems failure was a complication we wanted to ensure wouldn’t happen with any future malfunctions.
Simple Software Analysis Wasn’t All That Was Needed
The site was in such a state of disarray, it was difficult to pinpoint which devices were where and what each control panel specifically handled. Because this assessment really could have been used twenty years ago, and a number of devices had been added as a stopgap, there was nothing else to do but start from the beginning and walk the facility, visually mapping out what they currently had.
When a facility is working with a piecemeal system that has been built and hobbled over many years, even viable equipment may not function correctly due to a cascade effect from a simple issue – like the network switch. Mapping out the current system gave us the ability to look at all the crucial points of risk.
The Team Decided it was Time for a Control Systems Upgrade
While assessing their site, it was determined that they were running on an outdated software platform that would make it difficult to perform the upgrade they so desperately needed to get their facility on a SCADA system where everything could be centrally monitored.
Because they were so eager to be involved in each step and open to collaboration, it was much easier to identify their wants and needs while working with the maintenance techs. We designed a new integrated controls system that streamlined and simplified their processes according to what their biggest must-haves were.
IT/OT Risk Assessments Allow Companies to Plan for the Future
To make sure this momentum is carried through the entire process, communication and collaboration was maintained from the plant level through corporate leadership to ensure all wants and needs were communicated and executed. Close collaboration with employees allowed us to ensure this facility received the optimization it truly needed and could perform its day-to-day operations worry-free.
Every IT/OT risk assessment is different depending on the company, facility, industry, and scale. While it can get complex in situations like this one, where current building controls systems were, at best, hanging on by a thread, a thorough risk assessment with the input of the client allows E Tech engineers to design a custom automation solution perfectly-tailored to their present needs with an eye on adaptability for the future.
To learn more about IT/OT Risk Assessments follow the link below.
Begin Your Journey to Industry 4.0
Download our Beginner’s Guide to IT/OT Assessments to gain an understanding of what an IT/OT Assessment is, its benefits, and how to get started today.