E Tech Shares: Fact or Fiction: Debunking IT/OT Industrial Network Security Myths Webinar
E Tech Group invites you to join us for an informative and free webinar titled ‘Fact or Fiction: Debunking IT/OT Industrial Network Security Myths.
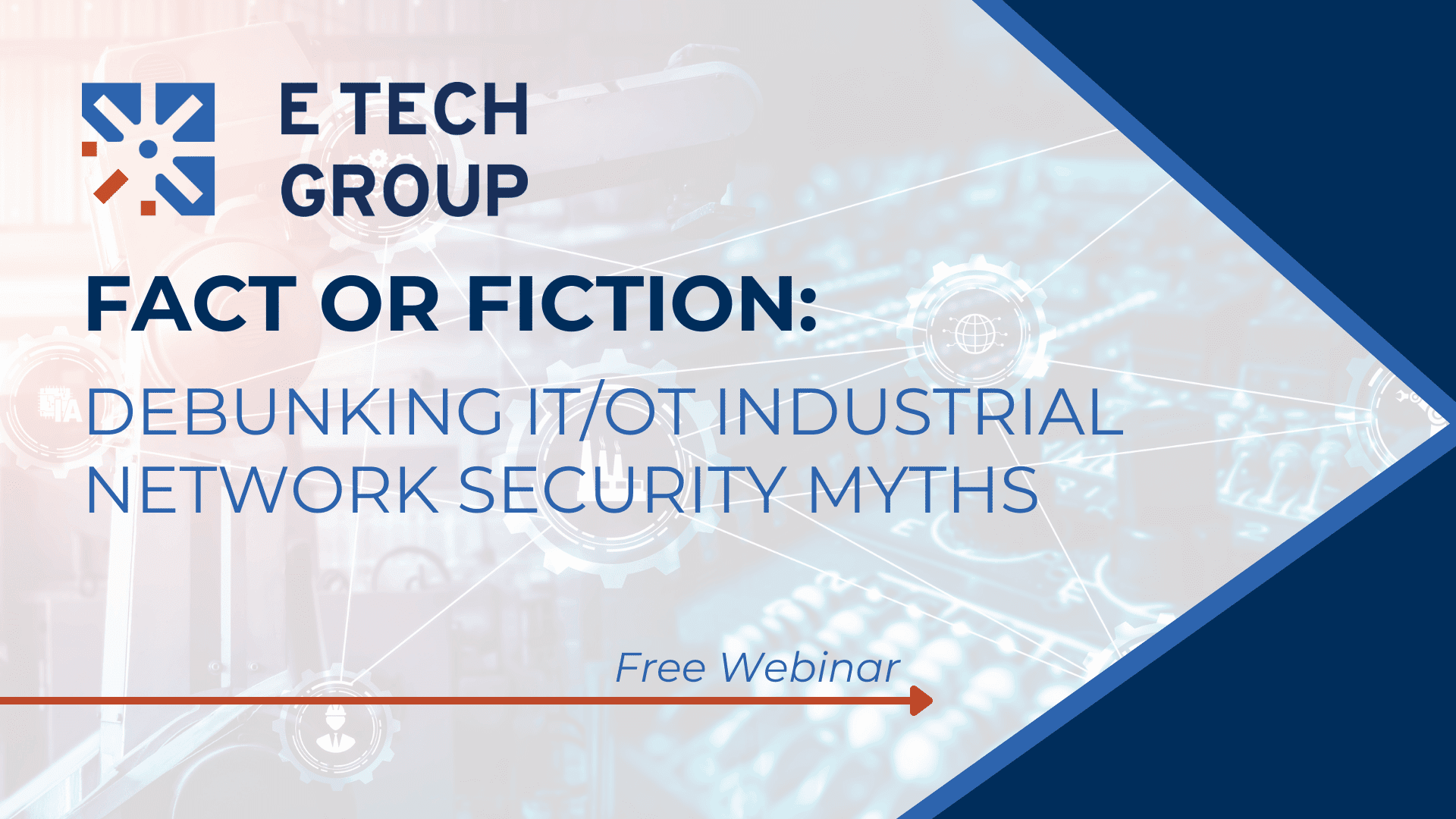
We’re your source for automation news. Keep up with the latest industry updates and E Tech employee spotlights, as well as tips and guidance from our manufacturing experts.
E Tech Group invites you to join us for an informative and free webinar titled ‘Fact or Fiction: Debunking IT/OT Industrial Network Security Myths.
The new office will create growth opportunities and allow E Tech Group to contribute to the innovative ecosystem of the Research Triangle, providing proven automation solutions to clients.
We are partnering with Rockwell Automation on the launch of their new FactoryTalk® Optix™Portfolio: Revitalize Your HMI Operations webinar series. The third and final webinar in this series is coming up in August- the first two are available OnDemand. The series is about how the FactoryTalk® Optix™ end-to-end HMI solution can revitalize HMI operations across the equipment lifecycle.
In late 2023 E Tech Group acquired Automation Group, and the team has now fully integrated into the E Tech Group brand. Adding Automation Group has allowed us to expand E Tech Group’s market-leading positions in the automation of Life Sciences, Food and Beverage, Consumer Packaged Goods, and Data Center industries. While adding additional resources and expertise in cybersecurity and big data.
E Tech Group © 2024 | All Rights Reserved.