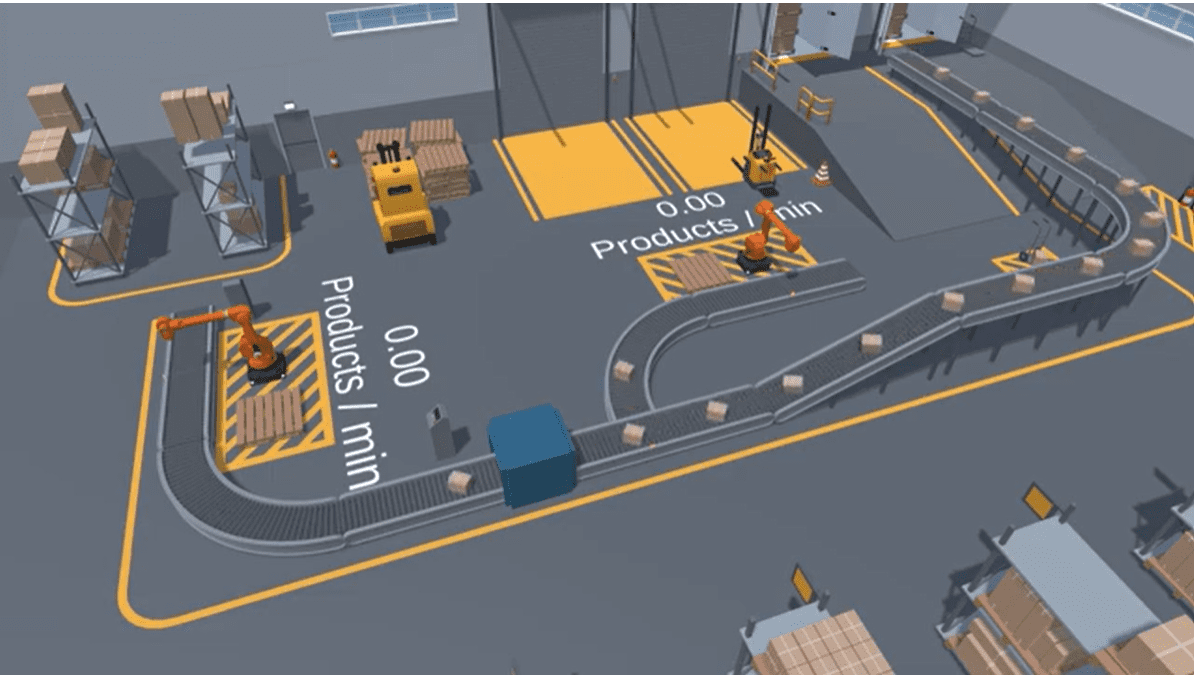
Modern production lines are highly sophisticated, and some can be large, encompassing hundreds of square feet. Due to their size and complexity, maintaining and troubleshooting these systems is more difficult and requires an increasing amount of expertise on the part of automation integrators.
With so many processes to coordinate and monitor, operators need control systems that provide a high level of assurance that processes are being accurately exacted, data collection is comprehensive, and communication between physical assets is effective.
The challenge is to create an intelligent, interconnected system which provides its users with immediate and actionable feedback. One method recently developed by the automation engineering field is a virtual model of the production lines called Digital Twin.
VIDEO
A Discrete Industrial Doppelgänger
With the advent of IoT technologies, we can connect devices on our clients’ production lines into a centralized control system that collects and analyzes data, and then use that data to simulate real-world processes in real time. This virtual model acts as a constantly-updated counterpart, mirroring the real-world entity in terms of its design, performance, and operational condition.
Here’s a breakdown of what that means:
The first component is the physical asset. This can be anything from a single machine or device to an entire factory or infrastructure network. The counterpart is then created. This is a virtual replica of the physical asset, which is often created using 3D modeling software and incorporating AI and machine learning so the digital rendering possesses the same abilities as the equipment it’s mirroring.
Sensors are attached to the physical asset collect real-time data on relevant parameters, such as specifications for automated palletizing or temperature in an automated pharmaceutical factory. This data feeds into the digital model. The data is analyzed and used to update the digital model, allowing simulations and predictions about the physical asset’s behavior.
The Crucial Relationship with IIoT
There’s another component that is critical to effective application of Digital Twin: the network where all this data is being monitored, collected and relayed. IIoT is what provides the communication infrastructure and data collection capabilities required to connect physical assets to their digital counterparts.
Sensors, controllers, and communication gateways collect data from physical assets and transmit it to the cloud or on-premises data platforms where the digital model resides. The dual physical-virtual nature of this process, coupled with the ephemeral nature of “the cloud”, makes adept control system integrators essential players in the application of this technology.
Process automation solutions that utilize Digital Twin must be comprehensive, with redundant network security measures and HMIs that make operation, data extraction and presentation, and system reconfigure simple for the user.
Benefits of Digital Twins for Manufacturers
This practice of creating Digital Twins enables us to provide operators with a tool which supplies insight on their processes. From mechanical jams to downtime metrics, users can peek under the hood of their process and take meaningful action.
Furthermore, because this system and its data are centralized, users can connect from anywhere, enabling remote support and troubleshooting without incurring the burden and cost, both in time and money, of traveling to the site.
Manufacturers can benefit in several ways from this ability to have 100% visibility of huge, intricate production lines that are impossible to monitor comprehensively from the factory floor:
- Improved Monitoring/Optimization: Digital twins provide real-time insights into asset performance, enabling better monitoring, predictive maintenance and optimization of operational processes.
- Less Defects/Downtime: By identifying potential issues early on, digital twins can help prevent equipment failures and unplanned downtime, leading to cost savings.
- Enhanced Design/Testing: Simulations on the digital twin can inform design decisions, test new configurations, and optimize processes before implementing them in the real world.
- Better Collaboration/Decision-making: Shared access to a digital twin facilitates collaboration between engineers, operators, and other stakeholders, leading to informed decision-making.
Digital Twin: The SparkNotes
While implementing Digital Twin at your facility isn’t essential to success, there is no question it augments the abilities of advanced integrated control systems.
Digital Twins:
- Gather data from any connected machine.
- Create a digital representation (“twin”) of machines.
- Use gathered data to actuate twins.
- Provide user-friendly display of production state.
- Show digestible metrics for easy diagnostics.
- Aid in remote support / troubleshooting
By holding a virtual mirror up to a production line, operators can see the details of what, how and where there is opportunity for improvement, which is integral to remaining competitive in ever-changing industries with ever-evolving technologies.