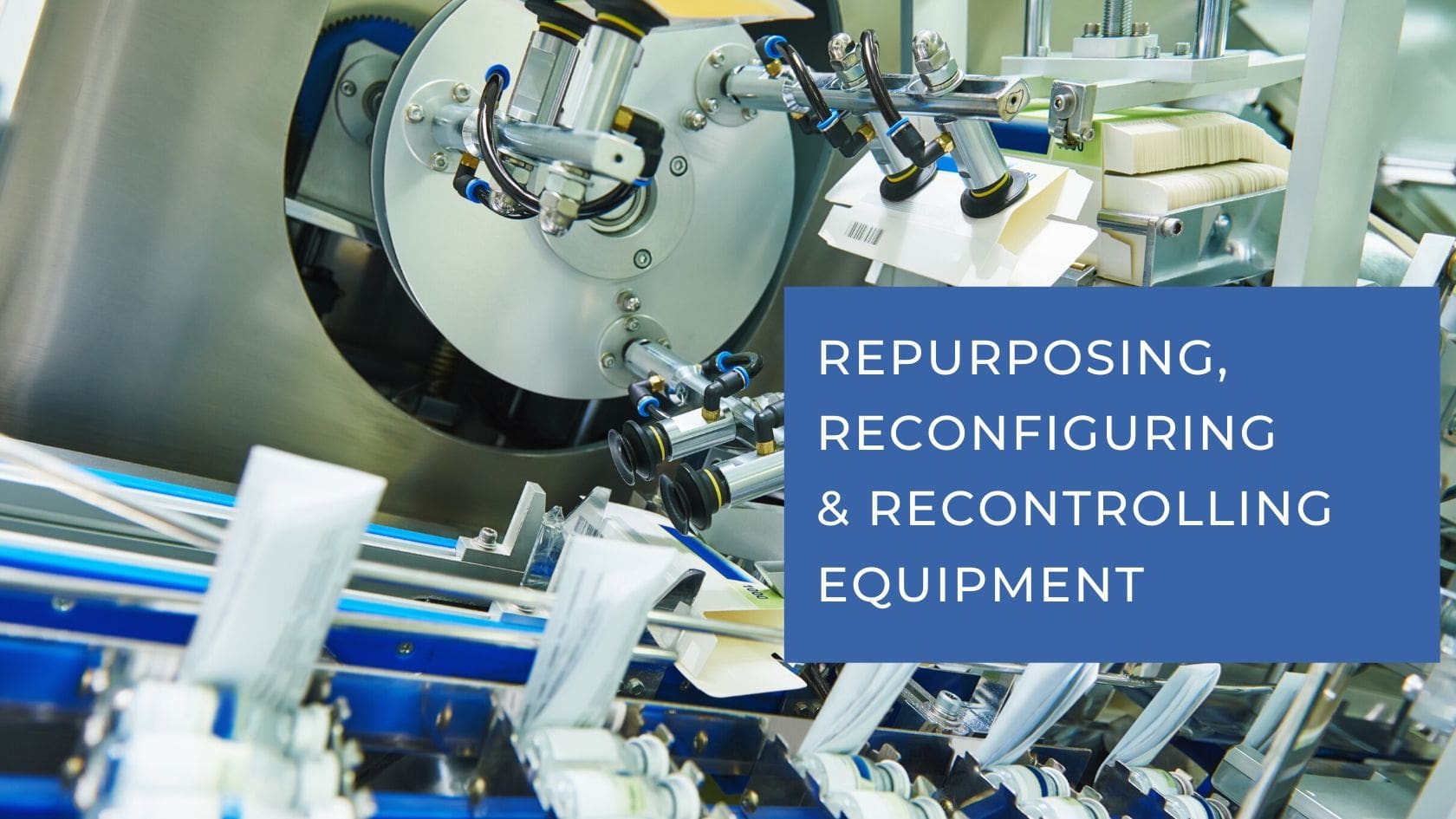
You may need to reconfigure some of the equipment in your facility for a variety of reasons. Corporate standards change, production goals increase, and demand can fluctuate, sometimes at lightning speed.
E Tech Group has completed hundreds of control systems upgrade projects like these for manufacturers in various industries, and over the years we’ve learned what it takes to make a reconfiguration or recontrol project successful. It starts with a clear and confirmed understanding of the goals and scope of the project, as well as the ever-important value of time.
Here, three E Tech Group employees share their experience on what contributes to the success of a machine repurpose, reconfiguration or recontrol project.
What’s the Ultimate Goal/Objective of the System Recontrol?
This may seem obvious, but often, folks don’t dig deep enough into looking into the WHY of the project. You can know you need to make a change, but it’s not going to happen without a solid business case. That business or use case not only justifies the cost of the automation solution; it can make the solution itself better by introducing new functionality and reducing risk.
“Are you going to be able to make more product, faster? Different things? Need to be more flexible? Your project may look different depending on the goal,” says Derrick Colyer, Business Development Manager. “Is it going to fix a problem and/or make it run more effectively?” Successful projects continue to use these goals as guidance throughout the course of the project – and after.
What is the Scope and Budget of the Project? 8 Key Factors for Success:
The goals help identify the business case and establish the priority, but setting a budget and assessing risk are part of the deeper work to be done when defining the scope of the systems upgrade. In looking back on successful projects, we identified these 8 key factors:
1. Project Team
The size of the team and task assignments will vary based on the complexity of the project, but at a minimum there should be an Executive Sponsor and Project Manager identified, and working members to address engineering, maintenance, human resources, safety, and operational requirements. The diverse perspectives and early engagement result in a higher value and lower risk design, and Executive Sponsorship provides business level direction and support on funding.
2. Process Control Structure
“Sometimes the client only wants to use one platform. Sometimes we retrofit to meet new corporate standards,” says Lee Schulte, HSE Machine Safety Programmer. Weighing factors such as the ability to support and maintain the system locally, manufacturer quality and support, delivery, pricing, and programming all contribute to the final decision.
3. Compatibility
“Some plants have several pieces of equipment coming from different vendors, and they use an integrator like E Tech Group for automation oversight to ensure that the pieces of equipment will communicate with each other,” Lee says. In addition, sometimes standardization work needs to happen so that all screens will look the same.
There’s also a safety consideration when it comes to compatibility. “If you have an emergency stop on one machine, you need it to communicate with the other equipment so that they know what to shut down,” Lee says. Skilled engineers will ensure any seemingly disparate pieces of equipment can be integrated under a controls system that allows them to properly communicate.
4. Age of the Equipment
“Is the hardware antiquated? Older Windows operating systems, for example, no longer have support and security patches. Older PLCs that are running out of memory space. Computing process power. Reliability issues. If you don’t think about these things at the beginning, then you may find yourself replacing something unexpectedly during the middle of the project,” Derrick says.
With aging equipment comes security vulnerabilities, Lee warns: “It used to be that there were no security issues in control systems. Now we’ve seen hackers getting in and shutting operations down. That’s a very real danger,” Lee says. “Now companies are thinking a lot more about cyber security as it applies to machine control. That’s another good reason to look at an upgrade.”
IT risk assessment and security solutions are well within E Tech Group’s automation design capabilities.
5. Certification Requirements
If you are subject to compliance by an outside organization (FDA, USDA, etc.), or have internal corporate standards, the tasks, responsible person(s), and time needed for certification or validation will be part of the scope. However, because these occur later in the project, during testing and commissioning, they are at risk of being rushed or understaffed due to earlier budget overruns.
Requirements should be considered at the outset of the project, and they should be revisited throughout the project, especially when there is a scope change. This ensures that the system upgrade is completed in a way that will keep the equipment processes compliant even with future changes in regulations.
6. Safety
“Safety is usually the last thing folks think about. You should be defining your safety needs during requirements specification, rather than at the end,” Lee says.
“Also think about the physical equipment itself – what it was designed to do and what its capabilities might be. If you change it, think about what’s at stake from a safety standpoint. There may be ergonomic considerations that need to be made with a reconfiguration, for example.” Laurie says.
If you have a safety engineer on staff at your facility, engage them early on during this scope definition process and get their input. If you don’t have a safety engineer on staff, work with your integrator early on to define safety requirements and consider conducting a full safety risk assessment.
7. Who’s Going to Use the Equipment?
You need to engage operators while defining the scope of your reconfiguration project, Derrick says. “Often, E Tech will do investigation for clients and get feedback from operators – both positive and negative,” he says. “Talking to the users and getting their input can be extremely valuable to use as a part of the solution development.”
There may be more requirements based on your workforce, says Laurie Cavanaugh, Business Development Manager. “If there’s a union, what are the requirements that need to be considered for workers using and maintaining the equipment,” she asks.
8. Training
“You want to train users so that they’re knowledgeable and autonomous,” Derrick says. “You also want to train them on how to engage with partners like E Tech Group. It’s all about empowering your staff. If we’re able to help companies be more self-sufficient and more effective on their own, that’s great.”
An important value in all of E Tech’s projects, whether new builds, retrofits or control systems upgrades, is working with the client throughout the entire process. This ensures that, by the time we get to training users on the new integrated system setup, they’ve got the background knowledge of the process and applications to manage the new automation design without the intervention of our engineers.
The Cost of Time: When does the Recontrol Need to be Completed?
“Time=money,” Laurie says. “In biotech, getting the project done a month early can mean millions of dollars in revenue or a competitive advantage. Even if it costs more, selecting a proven integrator with a larger team that can get it done is well worth any extra cost.”
More often, there is a balance between time and cost. You can save money by extending the schedule, keeping the team minimal, and working both on- and off-site, she says. Benefits are delayed, but still realized. And the smaller team working more cost-effectively meets the budget needs defined early in the project. What does time get you for this project? Debate it early, put a value on it, and revisit it throughout the project.
Don’t forget commonly overlooked factors like internal bureaucracy and commissioning, warns Lee. “There can be so much bureaucracy in some organizations that it can take weeks to get things done. Know up front how long it takes to get approvals for decisions and documentation. Commissioning can take more time than you think. Budget extra time for yourself to plan for any unknowns,” Lee says.