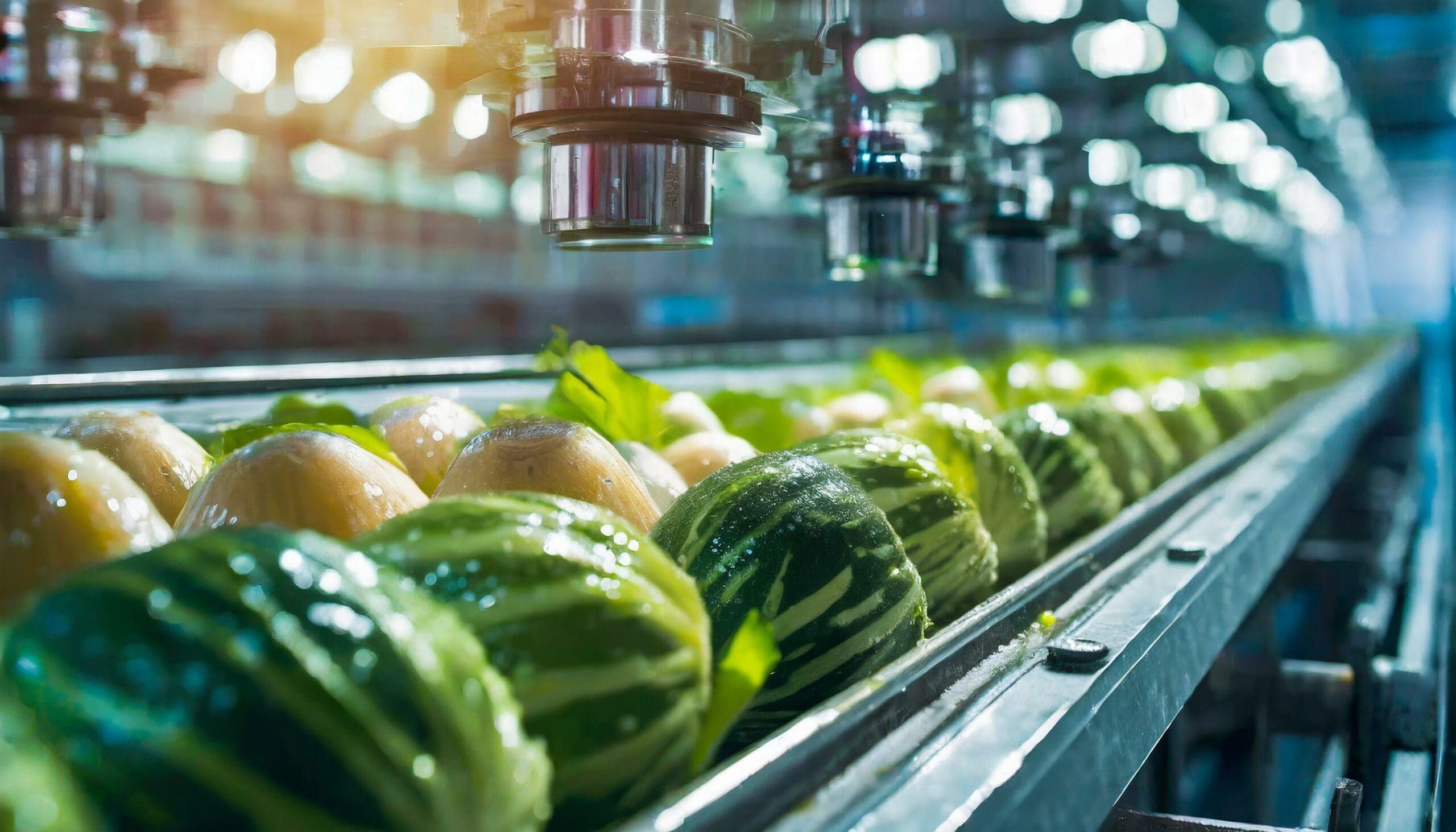
Author contributor: Vice President of Business Development, Laurie Cavanaugh
How to Transform a Legal Requirement into a Money-Making Tool That Drives Efficiency at Your Facility
In the food and beverage industry, genealogy and traceability is a legal requirement from the FDA. Contamination is a big problem in the food and beverage industry that tends to have a ripple effect. If your product is already in stores when contamination is discovered, it needs to be pulled from shelves before someone gets hurt. Worse, if your product is involved in other product supply chains – like a dairy supplier’s shredded cheese being used in other food products – then every product involved with that batch must be pulled. Hence why genealogy and traceability are important: the faster a contaminated batch can be identified and removed the better, avoiding additional harm and monetary losses. If you don’t have a monitoring system in place, you’re hedging bets against yourself and trying to recover from rather than prevent contamination issues.
Typically, the FDA’s genealogy and traceability requirement is fulfilled at the end of a process; this involves tracking raw products going into a final product. It could also involve extra steps like putting labels on products manually with dedicated labor, adding more cost to your production while also being constrained on the price that you can charge your customer.
Manual Labor Issues with Traceability and Genealogy
When your traceability and genealogy process isn’t automated, there are timeliness issues. The data is only as good as the batch time that was manually written down and keyed into a spreadsheet, and unfortunately, it’s prone to human errors. People can make transposition errors and if you suspected this, you would have no way to get a greater level of detail, which leads to a larger batch size for a recall.
Why not start at the beginning of your process and use that information internally to improve your operations? Automating this traceability and genealogy is often more cost-effective than manufacturers realize.
Leveraging Traceability and Genealogy Data to Your Advantage
A proper traceability and genealogy process will allow you to track your ingredients back to the source, such as a dairy being able to identify the specific farm and tanker of milk that was delivered.
When the genealogy and traceability process is automated, it involves implementing a data historian. The cost of a process historian is fairly inexpensive when you look at the amount of data it can collect. This information can do more than just track your mixed batches. The information you gain can allow you to make real business decisions that will lower your costs and improve quality. Here are examples of how the data can be used:
- Identify supplier quality issues – maybe you have a few suppliers that are consistently negatively affecting your batches
- Organic labeling – gain the ability to justify or approve your organic composition so that you can have a higher-priced product
- Recognizing trends – make your operators more knowledgeable and able to recognize trends and patterns more easily
- Bottlenecks – discover which parts of your process are causing bottlenecks
In addition to gaining better business intelligence, this kind of process data allows you to look at uptime and machine performance. You can now start to look at predictive maintenance to reduce unplanned downtime and do a better job of scheduling when it’s least likely to impact production. AI machine learning can continue to help identify patterns that a human operator may not be able to recognize.
It’s important to note that this advantage is not exclusive to food and beverage facilities in the industry with the most up-to-date equipment. If your facility is dealing with legacy controls and is currently working towards upgrading your machines, you can still automate this tracking process to start gaining insights.
Gain Better Quality Control and Efficiency at Your Food Processing Facility
Ideally, you can avoid outbreak and contamination issues by monitoring your process and quality issues. Thanks to your automated process, you can catch a bad batch before it even goes out your door. Gain better business intelligence, reduce downtime while maintaining uptime, reduce labor costs, and more by automating your genealogy and traceability processes.
If you’re interested in learning more about how this legal requirement can become a benefit to your facility, reach out to the E Tech team below.
Contact Us
"*" indicates required fields