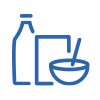
PLC Upgrade Improves Reporting, Visualization & Connectivity for Cheese Producer
A cheese producer contacted E Tech Group as they were facing a bottleneck preventing expansions. The project team installed a new panel to house the ControlLogix PLC and associated communications modules to reduce downtime.
The Project: Design a Flexible Control System that Allows the Client to Scale
A cheese production facility had three PLC5s critical to daily operations at full capacity, creating a bottleneck for an expansion of ongoing reporting projects. Acknowledging there was an immediate need to remove the existing PLC5s for a ControlLogix replacement, they contacted E Tech Group to facilitate the control system upgrade. Having worked with the customer on a CIP automation project, and their intimate familiarity with the three PLC5s, our team was already up to speed and could act quickly.
The Challenge: Upgrade, Integrate & Implement on a Tight Timeline
The project team had to determine physical and communication connections. The challenge was the existence of multiple DeviceNet networks to existing MCCs with legacy VFDs. Additionally, IO was dispersed over many areas, in multiple panels requiring process knowledge of the core of the facility.
Working with the exact opposite of a fully-integrated automation system inside of a 12-hour timeline to completion would require a creative approach to converting and integrating the new controls.
The Solution: Work With & Around Existing Automation Infrastructure
To minimize the downtime necessary to implement the new control system, all PLC5 IO racks were retained in place and a custom control system panel was designed and installed to house the new Controllogix PLC and associated communications modules.
During onsite support, the project team was able to convert a PanelView Plus that had previously been overlooked to the updated application communications. Our automation team had 12 hours to complete the conversion, which involved taking over existing IO, doing point-to-point checks and validating the HMI. This timeline would allow the client to begin their CIP process before production the next day, with the new ControlLogix installed.
IO Lists were developed to help with commissions, and detailed DeviceNet networks were documented. The team also solved challenges from non-default DeviceNet Node configurations and transitioning RIO communications to remote racks.
The Results: Scalability, More Data, Enhanced Visualization
The existing Wonderware Applications used for SCADA were updated by E Tech Group’s engineering team and communicated on the first attempt. The project team was able to meet and exceed the tight conversion schedule, with the customer beginning CIP sequences within 10 hours. Following these updates, the project team provided 48-hour continuous onsite support, available to assist with any immediate issues. With this project completed, the customer was able to benefit from the improved reporting, visualization and connectivity with the upgraded PLC system.
Contact Us
"*" indicates required fields
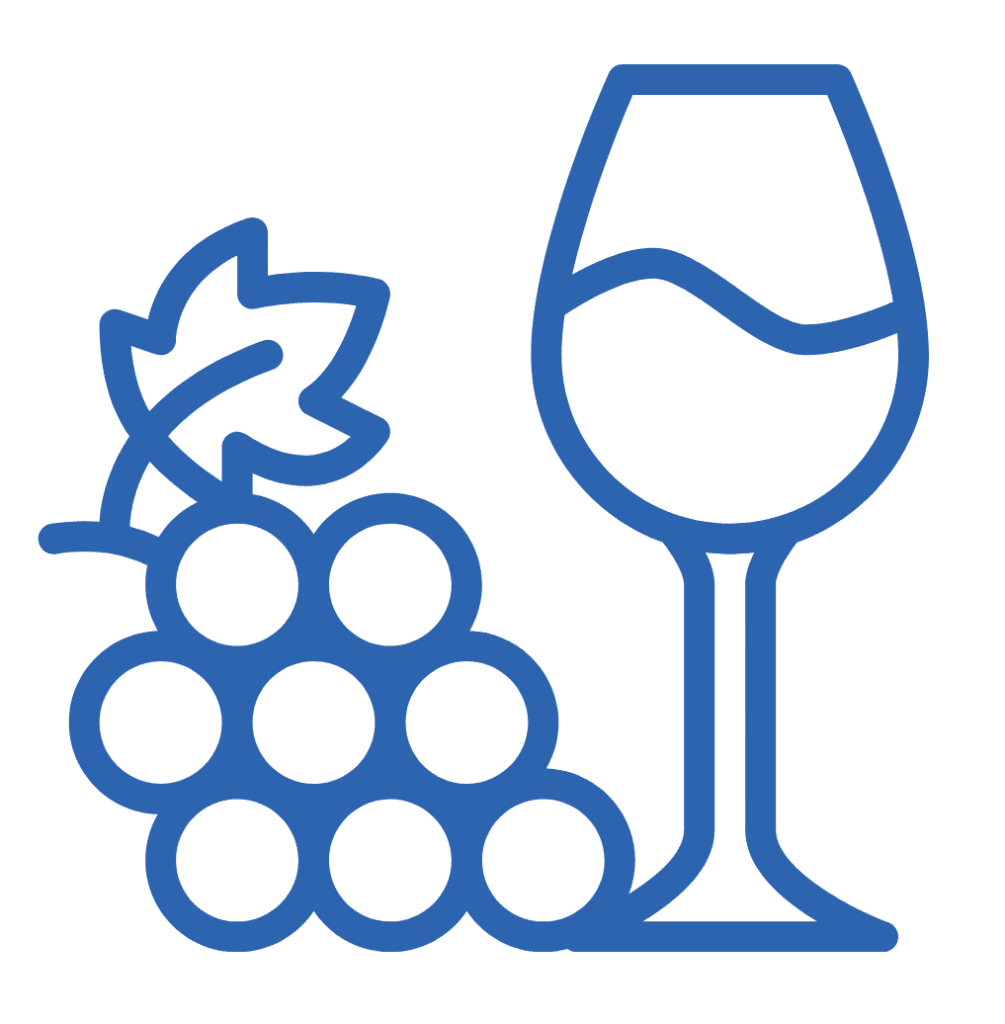
PLC & SCADA Upgrade Improves Red Fermentation Process for Winery
A California winery faced challenges due to outdated controls, which caused downtime, expensive hardware replacement, and lack of maintenance knowledge. They hired E Tech Group to create a PLC and SCADA upgrade solution.
The Project: Provide a Legacy Winery with an Updated Control System Solution
Outdated controls can pose many operational challenges. Companies that operate with outdated controls often experience frequent downtime, expensive or obsolete hardware replacement parts, or few personnel with the knowledge to perform maintenance on legacy systems. These challenges were faced by a long-running California winery that needed to modernize the controls for their red fermentation process. The winery needed to address how a control system upgrade would impact their operations and contracted E Tech Group to create a PLC and SCADA upgrade solution.
The Solution:
The first step was to create a well-documented project plan. E Tech Group analyzed the existing system design and detailed existing hardware components, software configurations and network connections. This step was crucial to have an accurate picture of their current control environment to mitigate production impacts during the implementation phase.
The project team upgraded hardware and reconfigured the customer’s existing Ignition SCADA automation software for seamless post-upgrade operations. The original red fermentation process was conformed with three areas: pump over area, continuous press area, and decanters area.
Previously, each area had their own PLC. The upgraded control system connected an Allen-Bradley ControlLogix PLC as the main controller, and remote IO was added to control the three areas into one. The system was programmed with ladder logic to the customer’s existing Ignition SCADA software, and seven new PanelView Plus HMIs were also programmed with FactoryTalk View ME as the client’s choice of visualization software.
The Results: Instant ROI with Improved Fermentation Uptime
The project team leveraged their PLC programming, Ignition SCADA software, and controls engineering expertise to resolve software compatibility issues, bugs in the programming code, and electrical connection challenges. E Tech Group’s automation team supported the project to resolve these challenges and performed extensive testing. With the PLC and SCADA upgrade complete, the client was able to improve the uptime of its red fermentation process and eliminate the key challenges of legacy system maintenance.
Contact Us
"*" indicates required fields
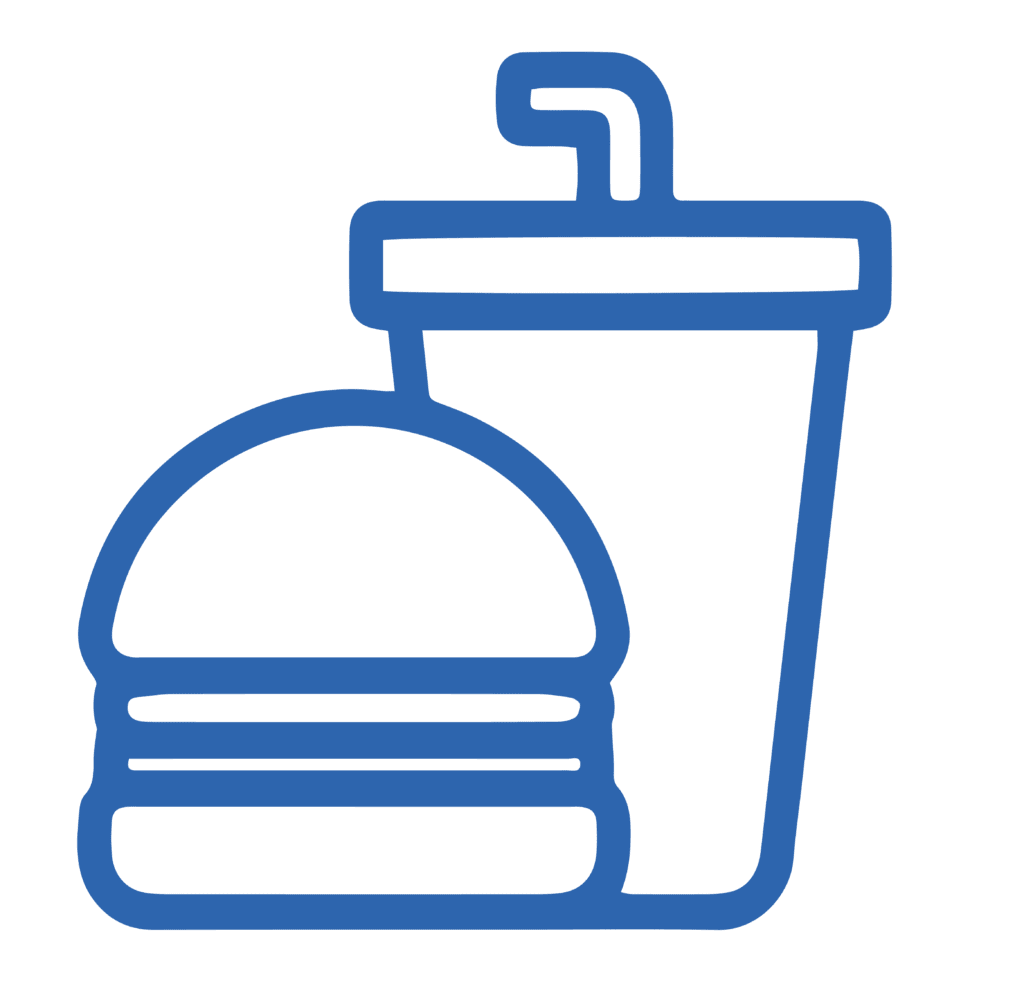
Designing a Flexible, Scalable Automated Processing System for The Better Meat Co.
The Better Meat Co. collaborated with E Tech Group and Barnum Mechanical Inc. to design, build and automate a full-scale processing system that has been successful in producing on-demand production and is scalable for future growth.
The Project: Turnkey Factory Automation for Mycoprotein Production
Food and beverage automation is changing, because so is the way we’re looking at industrial food production. The Better Meat Co. is a leader in the alternative protein movement. They produce a plant-based mycoprotein made by fermenting staple agricultural ingredients and minimally processing them into a dense protein that can be used in tandem with or instead of true meat. Their brand of alternative meat production touts:
- Whole food with natural texture of animal meat
- Complete amino acid profile
- Sustainable production, ethical alternative
- Cheaper than beef
- Much smaller carbon footprint than raising traditional meat
The Better Meat Co. faced a quick turnaround to full-scale production once they cleared the necessary regulatory barriers. Knowing they would need a robust, foolproof automation system to achieve their goals, they partnered with E Tech Group and Barnum Mechanical Inc. to design, build, and automate a full-scale processing system at their new mycoprotein fermentation facility in Sacramento, California.
The Process: Build & Integrate a Custom Automated Fermentation System
The Better Meat Co. partnered with Barnum and E Tech Group to build a full-scale processing system from scratch. The project team assessed existing equipment and current system requirements, and collaborated with various stakeholders to best design the full-scale processing system, keeping alternative meat processing standards and scalable performance capabilities top-of-mind.
E Tech Group’s team leveraged their expertise in automated control systems and process design to create a custom solution. The project team accomplished a software redundant control system that was capable of developer remote access support, redundant databases, recipe controls, historic data logs, and interactive reports.
The system that Barnum and E Tech Group helped to build allows The Better Meat Co. to experiment simultaneously with different types of feedstocks so that they can sterilize different media to run different types of fermentations.
The Result: A Better Way to Process Proteins
The Better Meat Co. implemented an automated system, developed with the help of E Tech Group and Barnum Mechanical, which has been successful in producing its products on demand. The CEO of The Better Meat Co. endorsed the value of automation. The system has been reliable since its deployment and is scalable for future growth.
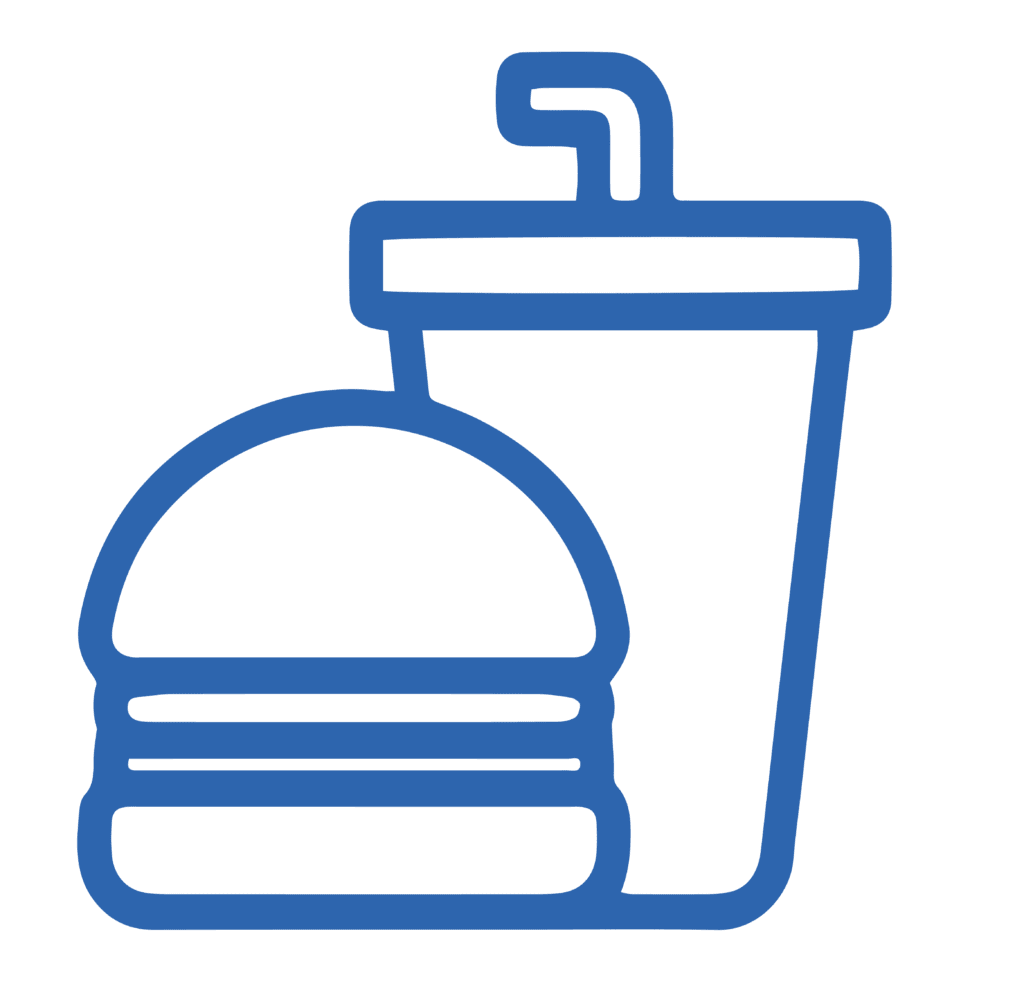
Utilizing Ignition Platform to Provide Organization-Wide Access to Quality Data
E Tech Group helped Prima Frutta increase productivity by 50% without hiring extra personnel by using the Ignition platform, which allowed remote operation of the production line and real-time data access from any smart device.
The Project: Ignite Increased Productivity with the Right Automation Platform
Manufacturers are facing costly workforce challenges. Between the labor shortage and the costs associated with employee turnover, companies are finding it difficult to increase productivity on their current automation system designs.
Prima Frutta, a cherry packaging facility in Linden, California, was struggling to maintain its production levels, but did not have the scope to add a lot of extra personnel to reach those levels. E Tech Group was called to help overhaul their control system, and under a tight timeline.
The Solution: Divide & Conquer Material Handling Automation
This control system upgrade was divided into three phases:
- Phase One: Project Planning and Documentation
- In the project’s first phase, the E Tech Group and Prima Frutta teams collaborated on planning, budgeting and documentation. They used CSIA methodologies and standards, created a detailed budget, and documented all OEM hardware into schematics that were approved before proceeding to Phase 2. This ensured the project remained on track and within budget.
- Phase Two: Wireless Network Set-Up
- The E Tech Group team successfully established a wireless network, which enabled ten tablets to remotely operate the production line through the Ignition industrial application platform from Inductive Automation. Ignition was chosen because of its flexibility, affordability and fast setup. The applications can be entirely customized quickly and easily, and data can be accessed from any smart device, including tablets, desktops, or any other smart device to allow real-time data access from anywhere the user is located.
In this project, the tablets enabled a change in process flow from anywhere in the plant, providing full SCADA control, unlike a static location. The installation process of Ignition on the tablets was seamless and took less than two hours. The Ignition software also ran on more than 120 screens throughout the plant, providing real-time data and color-coded information to employees for quick and efficient reactions.
- Phase Three: Development, Testing and Implementation
- E Tech Group used Prima Frutta’s existing server to develop modular software and PLC codes, allowing for quick deployment through component, template and user-defined type reuse.
The Result: Reaping the Fruits of a Well-Designed, Fully-Integrated Control System
The project resulted in a 50% increase in production with no additional personnel, helping Prima Frutta become the world’s largest cherry production line. The Ignition platform reduced downtime and enabled the facility to respond to changing conditions.
Contact Us
"*" indicates required fields