A PLC-5 to ControlLogix conversion within 48 hours helped improve control and visibility for a food manufacturer’s conveyor system.
Challenge
Challenges arise when hardware and software become outdated. This was the case for a leading food manufacturer who needed modernized controls for their warehouse conveyor system. The existing Allen-Bradley PLC-5 hardware was obsolete and lacked modern communication protocol. The conveyor system also lacked HMIs to monitor processes, identify problems, and visualize data. Because of this, the customer sought the help of E Tech Group, an E Tech Group company, to upgrade their Allen-Bradley PLC-5 to the latest Rockwell Automation ControlLogix processor, integrate AVEVA InTouch HMI stations, and connect devices over an EtherNet/IP communication network.
Solution
E Tech Group was challenged to migrate the PLC system within 48 hours of planned downtime. E Tech Group worked closely with the customer to understand their existing system in detail and identified potential challenges that could occur before the PLC conversion. After this step was completed, E Tech Group proceeded with the Allen-Bradley PLC-5 to ControlLogix migration, overseeing the installation and testing. E Tech Group converted the existing PLC-5 logic to its Logix equivalent and connected the new ControlLogix processor to distributed, remote, and POINT I/O racks via EtherNet/IP communication network. Then the project team configured and connected devices with AVEVA InTouch HMI to provide conveyor line operators with better visualization capabilities.
Results
This upgrade provided the food manufacturer and its operators with greater control and visibility over their conveyor system, enabling efficient fault detection, improved PLC and HMI communication, data acquisition, and technical support from the manufacturer. With this migration project completed, the customer minimized their risk of downtime, enhanced conveyor performance, and strengthened their network communications.
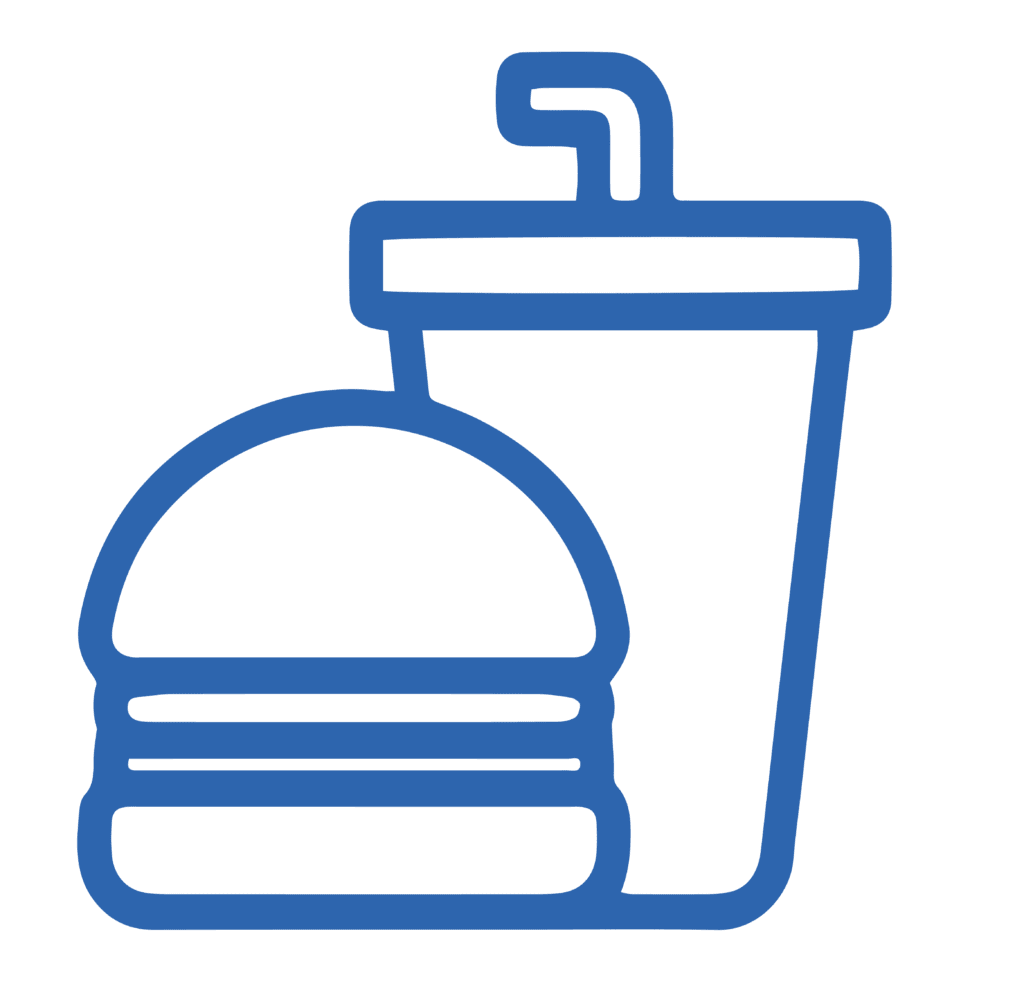
PLC-5 to ControlLogix Migration Supports Greater Uptime for Global Spice Supplier
A global supplier of spice ingredients needed to upgrade their Allen Bradley PLC-5 system. E Tech Group was recruited to modernize their obsolete PLC system to a more IIOT-friendly platform.
The Project: Remove Production Constraints with Complete Control System Upgrade
A global supplier of spice ingredients needed to upgrade their 25-year-old Allen Bradley PLC-5 system. The outdated platform was experiencing constraints and was limiting network connections. The client was seeking a system integrator that could provide timely PLC migration support using the latest technology available.
Automation Group, an E Tech Group Company was recruited to modernize their obsolete PLC system to a more IIOT-friendly platform. Automation Group, E Tech Group’s most recent acquisition, is a leading provider of automation services. They’ve worked with over 1000 clients across North America, implementing advanced control system solutions tailored to each facility’s unique challenges.
The Solution: Implement an Integrated, IIoT-Compatible Control System
E Tech Group automation professionals reverse-engineered the customer’s legacy system and analyzed existing diagrams to identify potential risks to obtain detailed information on device and wiring configurations. This step was crucial to improve control system performance and understand their control environment before moving to the design phase.
As a leading Rockwell Automation system integrator and CSIA-certified automation company, we developed a simplified migration plan using the latest technologies. We converted all networks to Ethernet/IP communications, upgraded the client’s PLC-5 system to ControlLogix and consolidated FactoryTalk View SE screens, making it easier for plant personnel to operate the system.
The Results: The First Step in a Digital Transformation
The global spice supplier’s upgrade from PLC-5 to ControlLogix was completed on schedule and improved performance, greater uptime, and a more user-friendly interface for the client’s PLC system. This upgrade project was a crucial step in the client’s digital transformation journey.
Our recent addition, Automation Group, an E Tech Group Company, designed and implemented this creative automation system solution. For more information on this control system upgrade, visit their website to read the complete case study.
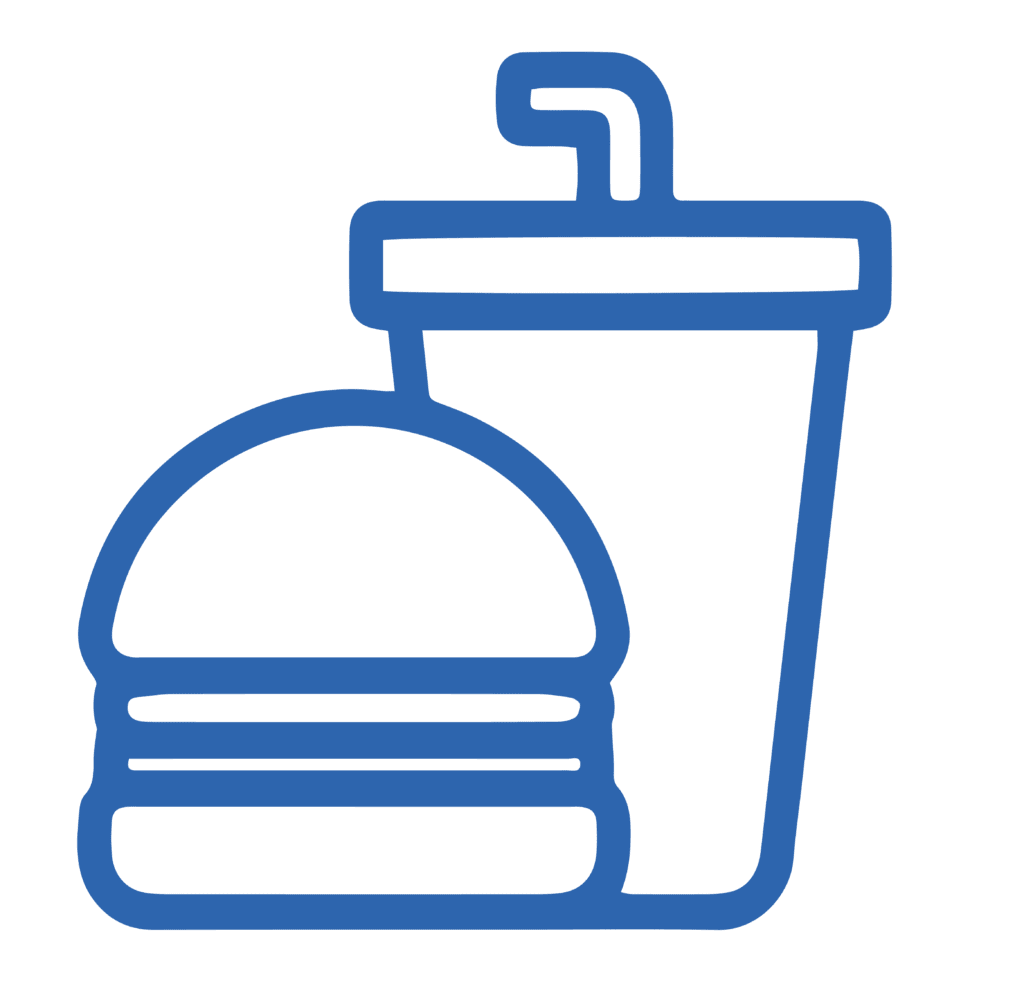
Major SCADA & PLC Upgrade Increases Uptime, Lowers Maintenance Costs for Rice Milling Company
A rice milling company needed a new PLC in a truncated timeline. Automation Group, an E Tech Group Company’s team inventoried equipment and upgraded the facility’s automation system to Ignition SCADA software, setting the client up to meet goals and be prepared for growth.
The Project: Upgrade a Facility’s Control System in 2 Days with No Downtime
A rice milling company was facing operational constraints of a legacy SCADA system. The system was costly to maintain, and the control system design caused frequent communication problems between different production areas.
The client needed a new PLC program to be installed within a 48-hour timeframe to minimize production impacts, and the existing SCADA system needed to remain operational during the migration to Inductive Automation’s Ignition platform.
The client contracted Automation Group, an E Tech Group Company as their choice system integrator given their advanced expertise in system migration and the successful execution of projects at the client’s other facilities.
The Challenge: Tread Softly with Time & Operation Constraints
There were a few obstacles to this control system upgrade that required one of the unique proficiencies of E Tech Group’s brand of automation system integration:
- An obsolete PLC controlled their rice finishing line.
- An obsolete SCADA automation application controlled the entire facility.
- The client had a strict 48-hour timeline to the upgrade implementation.
- The new SCADA needed to be implemented without disrupting the existing one.
- The new SCADA needed to be able to work alongside the legacy control system.
E Tech Group’s team knew this diverse set of obstacles would affect the course of the project, end-to-end. Our control system integrators had to find a creative way to work quickly without sacrificing our detailed approach or the quality of the upgraded automation system.
The Solution: Modular Migration Solves Everything
The project team created a site inventory of the customer’s existing PLCs, network, computers, and applications. The project included upgrades to servers, computers, and network switches in collaboration with the customer’s IT department, the upgrade to Ignition SCADA software across six applications with approximately 500 screens, and the upgrade to two ControlLogix PLC chassis.
The SCADA upgrade was completed in several phases and each application was upgraded individually. This helped minimize impacts on the customer’s production efforts and enabled the legacy and new SCADA applications to run simultaneously so the customer’s personnel could learn the new SCADA software.
The Results: Short-Term Success for Long-Term Growth
This approach to updating the facility’s control system allowed the client to improve operations and network communications at once while giving their operators time to learn the new system before getting rid of the old. Automation Group, an E Tech Group Company leverages this distinct diverse, multidisciplinary engineering approach to create intelligent automation solutions for the customer’s long-term success and the opportunity to support their operations in the years to come.
The talented automation engineers at our most recent acquisition, Automation Group, an E Tech Group Company, managed this particularly tricky project. For more information on this system upgrade, visit their website for the complete case study.
When a major food manufacturer needed an automation system integrator to design and fabricate six UL 508A custom control panels for their new production line, E Tech Group rose to the challenge, and in record time.
The Project: Fabricate Six Custom Control Panels on a Tight Timeline
A major food manufacturer needed a trusted control system integrator to design and fabricate six control panels for their new production line. They chose E Tech Group because of our expertise in building UL 508A control panels, including custom panel design, as well as our ability to source hard-to-find parts, and ability to create alternative solutions to meet tight project deadlines without compromising system quality.
The client required swift project execution and a customized automation solution that included 6 UL 508A control panels. E Tech Group was able to streamline the panel build process by leveraging E Tech Group’s proven project management methodology. E Tech Group rose to the challenge, constructing six UL508A control panels with speed, quality, and engineering integrity to support the customer’s new production line.
The Solution: Collaborate Closely with the Client from Start to Finish
A main challenge was to ensure the project remained on schedule due to long lead items to PLC components, such as safety PLC modules, VFDs, and other components necessary for this integrated control system solution. Our automation engineering team leveraged our efficient panel build process and AG5 project methodology to create a viable solution for the customer across five key phases:
Phase 1 – Collaborate, Plan & Prepare
Following a technical Q&A with the customer and creating a bill of materials, E Tech Group’s project manager collaborated internally with their purchasing department to review project materials and potential long lead items. Long lead items were ordered to ensure the project timeline was not impacted.
Step 2 – Design the Panels & Source the Parts
Next, E Tech Group’s engineering team created the control panel design, defining the system requirements, developing a device and I/O list, and creating the panel schematics. Every detail had to be considered and carefully planned to support proper functionality when the control panels were later assembled.
Our engineers and drafting team approved the control panel design with engineering leadership as part of our own internal quality control procedures before the panel design was submitted for client approval. E Tech Group’s purchasing department then ordered all automation hardware to support the multiple control panel builds.
When supply chain issues were identified, we quickly informed the project team of unavailable materials to discuss possible alternatives with the client. E Tech Group’s project manager and engineering team worked closely with the client to create a viable food and beverage automation solution with compatible alternatives. The team then regrouped internally to source those alternative hardware options with the purchasing department.
E Tech Group understands that the collaboration and design stages are key to the success of the next phase of a project – building the control panels. Attention to detail and quality control measures lead to faster and higher-quality project outcomes, which is why the first two phases act as a foundation to deploying a well-executed control system solution.
Phase 3 – Fabricating the UL 508A Control Panels
Once the schematics were completed and the components were received, E Tech Group began building the control panels at their large-scale panel shop in Modesto, California. The panel shop team assembled the six control panels to the customer’s specifications and to comply with UL 508A standards. The panels integrated CompactLogix 5380 Controllers with POINT I/O Safety I/O Modules, PowerFlex 525 AC drives, and Panel View Graphic Terminals for visualization.
Phase 4 – Testing the Assembled Control Panels
E Tech Group’s control panel shop team carefully evaluated each aspect of the assembly process to ensure it complied with safety requirements and functions as intended. The panel shop team performed several evaluations, including point-to-point testing, and produced documentation for the client of how the control panels were built in collaboration with E Tech Group’s drafting team.
Phase 5 – Deploying the Panels to the Client
With the control panels thoroughly tested and validated for complete functionality, E Tech Group prepared and shipped the control panels to the client’s site for installation.
The Results: An Advanced Automation Solution Delivered Ahead of Schedule
E Tech Group’s multidisciplinary team showcased exceptional results in this project execution, completing the project 4 weeks ahead of schedule. Through seamless collaboration and leveraging diverse expertise, our team achieved high-speed project completion, avoiding supply chain disruptions by sourcing alternative automation hardware without compromising control system or panel quality.
Our control system integration team’s coordinated efforts expedited the timelines, resulting in significant time and cost savings for the client. The emphasis on maintaining high standards throughout the project lifecycle ensured the delivery of quality solutions, ultimately leaving the client highly satisfied with the outcomes achieved for their new production line.