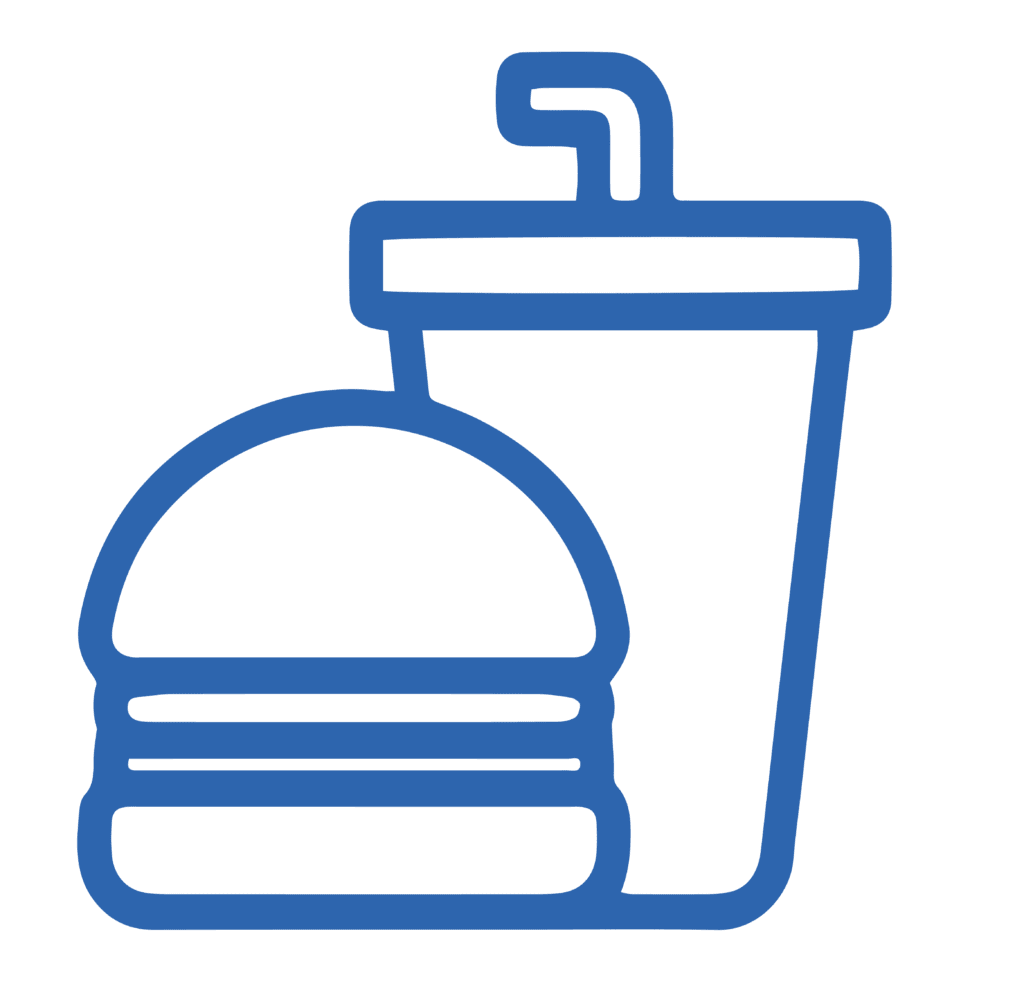
Rockwell Automation Solutions Improve Spice Company’s Production Capabilities
When a major spice producer decided it was time to convert key manual processes to automation in order to improve efficiency, E Tech Group leveraged Rockwell Automation solutions that supported increased throughput and cost reductions.
The Project: Design a Custom Automation System for a Spice Supplier
A supplier of culinary spices needed to automate their receiving and washing areas to improve efficiency and visibility. The existing manual approach caused bottlenecks and hindered production potential, making automation crucial for optimizing processes, streamlining workflows and gaining the ability to scale.
The Solution: Utilize Rockwell Automation Technology for Seamless Transition
E Tech Group used a range of Rockwell Automation hardware and technologies to align with the customer’s objectives, resulting in a more streamlined and responsive control system. They also upgraded the hot wash hardware using a suite of Rockwell Automation components, improving efficiency, reliability, and safety. Rockwell Automation’s Studio 5000 v33 and Factory Talk View Studio Machine Edition provided a user-friendly control system interface for the spice supplier.
The Results: A Cost-Effective Automation Solution with Real-Time ROI
Our automation and engineering firm provided dedicated support to the project, which resulted in increased throughput and reduced production costs. The expected return on investment will materialize in three years, showcasing the cost-effectiveness of the Rockwell-based automation solution. This transformation optimized operations and paved the way for future improvements, highlighting the effectiveness of our collaboration and Rockwell Automation’s process control solutions.
E Tech Group’s system integration expertise resolved complex integration challenges for a major food distributor, fostering trust and future collaborations with the customer.
Challenge
Challenges in complex projects are inevitable, but the dedication to overcome challenges is what sets exceptional system integration firms apart. This case study highlights how E Tech Group, stepped in when another company was unable to fully execute a project. The case study underscores how E Tech Group’s exceptional capabilities not only remedied the situation but also earned the trust of the client to support three additional projects to-date.
The client, a major food distributor, needed to integrate a conveyor system with their pocket filler, vacuum filler, and steamer. Delays in the system deployment resulted from understaffed control support, incomplete project aspects, and equipment transfers from another facility. Plus, new conveyors had been installed by a different controls integrator. The client sought E Tech Group’s help to create a clear project outline and overcome the project challenges.
Solution
E Tech Group staffed the project with highly skilled engineers with expertise in canning lines and control strategy. First, the project team examined the state of the production line to determine what needed to be finished. They discovered that the current contractors involved were facing too many challenges with the conveyors before the system could become operational and the project deployment lacked direction because of this.
E Tech Group’s engineers presented a 30 itemed punch list to the startup team which became the central punch list for the project. E Tech Group met with plant technicians to determine how the existing OEM equipment interlocks to the conveyor system and met with OEM experts to have a firm understanding of the pocket filler design. The conveyor company later left the site without completing their controls, which caused E Tech Group to create a controls strategy that integrated the conveyor system with the existing pocket filer, vacuum filler, and seamer. The project team corrected electrical issues, standardized the programming between each OEM equipment and conveyor system, and tested the system’s functionality including the customer’s existing Allen Bradley ControlLogix PLCs and PanelView Plus HMIs.
Results
By promptly tackling issues and implementing effective solutions, E Tech Group restored the project’s trajectory within weeks. The team’s expertise not only conquered challenges but also built client trust, leading the customer to engage E Tech Group for three additional projects to-date. E Tech Group rose to the occasion with system integration expertise and dedication, helping the client reach their goals and supporting positive project outcomes.
An efficient PLC and SCADA upgrade successfully minimized downtime, reduced costs, and improved the operational control of a tomato peeler system, enhancing product quality and competitiveness for a food manufacturer.
Challenge:
A prominent food manufacturing company specializing in tomato processing faced a significant challenge with their existing peeler system. The controls hardware was outdated, causing a higher risk of downtime, limited maintenance support, and poor controls performance and control network communications. The company needed to resolve these challenges and sought the support of E Tech Group. The food manufacturer chose E Tech Group for their proven track record and expertise in control systems, supporting a swift and successful automation project.
Solution:
The customer needed to upgrade their existing panel hardware for a modern EtherNet/IP control system. E Tech Group analyzed the customer’s existing system and provided the customer with a detailed plan to meet their specific needs of an upgraded system. This upgrade involved converting their existing Allen-Bradley PLC5 to the Rockwell Automation ControlLogix platform using the RSLogix 5000 programming environment. The customer also needed support connecting the ControlLogix platfrom to a new EtherNet/IP control network, converting several Powerflex VFDs with EtherNet/IP communications, and programming AVEVA HMIs and SCADA software for improved system visibility and real-time data monitoring. E Tech Group supported the system upgrade, retagging and remapping the existing logic to the new EtherNet/IP controlled hardware. The AVEVA HMIs and SCADA system were redesigned and programmed to provide the customer’s operators with better usability and improved access to critical data, ultimately enhancing their operational efficiency.
Results:
The project was completed on schedule, minimizing downtime. This led to significant cost savings as system failures were reduced. Improved control performance ensured smoother tomato peeler operations, enhancing the customer’s product quality. The enhanced system visibility enabled data-driven decisions and proactive issue resolution, reducing operational risks, and improving efficiency. Ultimately, this project supported the food manufacturer’s competitiveness in the market with a more modern control system.
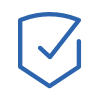
Improving Efficiency & Safety on a Food Client’s Conveyor System
A food production and distribution facility was experiencing frequent jams and safety hazards with their conveyor system. E Tech Group assessed and upgraded the conveyor with an MDR, increasing output, efficiency and safety.
The Project: Fix the Feeding Jams in a Food Producer’s Conveyor System
The freezer outbound ASRS section in a food production and distribution facility is responsible for moving products in batches of 16×2 cases across two lines. However, the client’s current system lacked accumulation feeding to the robot responsible for palletizing the cases, leading to frequent jams and safety concerns for operators who had to clear these jams.
E Tech Group’s automation team provided an assessment of the current issue and recommended the replacement of the existing thirty-foot conveyor on both lanes with a lane MDR (Motorized Driven Roller) conveyor to improve control up to the merge point.
The Challenge: Complete a Conveyor System Upgrade Riddled with Limitations
The replacement of the MDR section as originally described sounded like a straightforward solution, as it was a complete replacement. However, once our team began configuring/mapping out the process automation solution, they began encountering a number of challenges during the detailed design phase:
Limited Mechanical Drawings:
- Limited Information: The client lacked comprehensive details about the existing system, leading to multiple measurement trips to gather essential information.
- Incorrect Conveyor Size: Initial measurements indicated a 30 ft length, but it was later determined to be 31.5 ft, necessitating a revision of our order.
- Clearance Issues: The new conveyor, at 25 inches wide, didn’t align with the existing 20-inch-wide conveyor, requiring a cost-effective alternative solution. The partial removal of the old conveyor prompted a reconsideration of our strategy.
- Belt-Driven Upstream Conveyor: Discovering that the belt we replaced powered an upstream diverging conveyor, we had to relocate the replacement motor, leading to additional unplanned work.
Limited Electrical Drawings
- The onsite team had to rely on the existing panel to locate the power source, as they had limited electrical drawings.
Limitations on Conveyor Hanging
- The client specified that the E Tech Group team could not add additional support to the ceiling in hanging the conveyor, which would need to be 22 ft high and as floor-supported as possible.
- The requirement to use floor supports rather than ceiling support posed an engineering challenge left to the E Tech Group team to determine how to effectively support this system.
New vs Old Conveyor Size
- As the team was required to use floor support, a height-adjustable system was needed to provide the alignment from the old to new conveyor dimensions.
The Solution: Roll with the Punches & Add an MDR
E Tech Group’s expert automation team brought their deep domain expertise in food and beverage production systems, along with their innovative and cooperative approach to project management, to tackle the myriad obstacles to this critical conveyor system upgrade:
Overcoming Mechanical Limitations
To address the mechanical challenges, the onsite team initiated a collaborative effort across multiple departments to develop an effective design solution. They worked diligently to address and solve:
- Mechanical Footprint Design: Due to limited mechanical drawings, the team relied on precise hand measurements to establish the system’s mechanical footprint, serving as the foundation for the design efforts.
- Load Support Design: The team designed load supports tailored to the product’s weight and dimensions to ensure efficient custom
- Bracket Fabrication: For handling different conveyor sizes, the team created specialized brackets fabricated at a local machine shop to meet project-specific requirements.
- Height Adjustment Design: To align conveyor heights without adding ceiling weight, the team engineered special brackets. These brackets were pivotal in achieving height adjustment and managing floor support effectively.
Implementation & Benefits
After a series of trips to refine the design solutions, the E Tech Group onsite team successfully implemented the proposed changes. Once the remaining variables were addressed, the implementation process went remarkably smoothly. The key enhancement to this system being the incorporation of MDR (Motorized Driven Roller) accumulation, which added significant value to the system.
The implementation phase involved the following steps:
- Assembly and Installation: With the refined design in place, our installation team worked diligently to assemble and install the newly designed components. This included fitting the custom brackets, load supports, and the MDR accumulation system.
- Testing and Quality Assurance: Rigorous testing and quality assurance procedures were carried out to ensure that the system operated efficiently and safely. We paid particular attention to the seamless integration of the MDR accumulation, which played a pivotal role in reducing the risk of jams and enhancing overall system performance.
- Operational Efficiency: The new design and components improved the system’s operational efficiency. The added MDR accumulation allowed for smoother product flow, eliminating the frequent jams that had previously posed a safety concern for operators.
- Enhanced Safety: The implementation not only resolved the mechanical challenges but also significantly enhanced safety conditions for operators. With the reduction in jam-related incidents, the need for operators to intervene and clear conveyors was significantly reduced.
The Result: More Safety, Increased Throughput, No Jams
Once the designed installation was complete and operational, the successful implementation of the solution brought about positive change in the system’s efficiency and safety, as anticipated, mainly through the introduction of MDR accumulation.
This project exemplified E Tech Group’s ability to overcome intricate challenges and deliver an innovative solution that improved both operations and workplace safety.