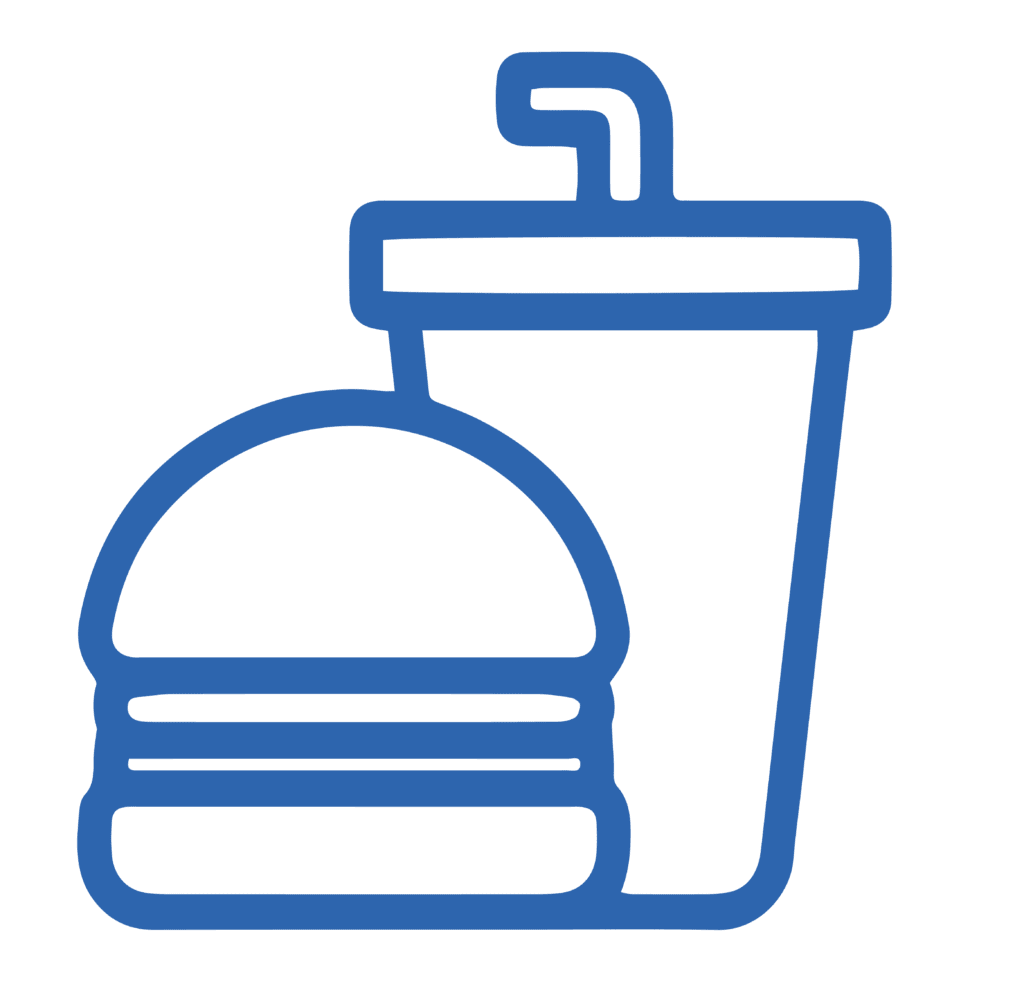
Designing a Flexible, Scalable Automated Processing System for The Better Meat Co.
The Better Meat Co. collaborated with E Tech Group and Barnum Mechanical Inc. to design, build and automate a full-scale processing system that has been successful in producing on-demand production and is scalable for future growth.
The Project: Turnkey Factory Automation for Mycoprotein Production
Food and beverage automation is changing, because so is the way we’re looking at industrial food production. The Better Meat Co. is a leader in the alternative protein movement. They produce a plant-based mycoprotein made by fermenting staple agricultural ingredients and minimally processing them into a dense protein that can be used in tandem with or instead of true meat. Their brand of alternative meat production touts:
- Whole food with natural texture of animal meat
- Complete amino acid profile
- Sustainable production, ethical alternative
- Cheaper than beef
- Much smaller carbon footprint than raising traditional meat
The Better Meat Co. faced a quick turnaround to full-scale production once they cleared the necessary regulatory barriers. Knowing they would need a robust, foolproof automation system to achieve their goals, they partnered with E Tech Group and Barnum Mechanical Inc. to design, build, and automate a full-scale processing system at their new mycoprotein fermentation facility in Sacramento, California.
The Process: Build & Integrate a Custom Automated Fermentation System
The Better Meat Co. partnered with Barnum and E Tech Group to build a full-scale processing system from scratch. The project team assessed existing equipment and current system requirements, and collaborated with various stakeholders to best design the full-scale processing system, keeping alternative meat processing standards and scalable performance capabilities top-of-mind.
E Tech Group’s team leveraged their expertise in automated control systems and process design to create a custom solution. The project team accomplished a software redundant control system that was capable of developer remote access support, redundant databases, recipe controls, historic data logs, and interactive reports.
The system that Barnum and E Tech Group helped to build allows The Better Meat Co. to experiment simultaneously with different types of feedstocks so that they can sterilize different media to run different types of fermentations.
The Result: A Better Way to Process Proteins
The Better Meat Co. implemented an automated system, developed with the help of E Tech Group and Barnum Mechanical, which has been successful in producing its products on demand. The CEO of The Better Meat Co. endorsed the value of automation. The system has been reliable since its deployment and is scalable for future growth.
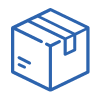
Supporting a Global Courier’s Ability to Scale with 24/7 Support
A global e-commerce leader wanted to add 24/7 support to several of their US facilities. E Tech Group’s infrastructure upgrades and added support in US-based sites paved the way for an international scale-up as multiple European sites were optimized.
The Project: Take 24/7 Domestic Control System Support International
E Tech Group had previously worked with one of the world’s largest e-commerce companies to upgrade and implement 24/7 support at a US facility. A few years after the completion of the initial project, the client implemented round-the-clock sortation of packages to keep up with demand. This compounded the time constraints associated with any interventions, and also increased the complexity of the system.
This switch to continuous sorting increased the number of calls to 24/7 support to maintain uptime at the first facility. This led to the client’s decision to add 24/7 support contracts across five additional US-based sites to support the switch to round-the-clock automated material handling.
The Challenge: Integrate SCADA Support Across Oceans
At the same time, E Tech Group developed and commissioned a SCADA environment for the client’s five largest European-based sites. These sites initially decided not to maintain a 24/7 support service contract because they were not experiencing the same delays as their US-based counterparts.
However, after the project support ended, the European sites ran into issues with their network communications, experienced power outages, and had issues troubleshooting due to the lack of knowledge about the software. This eventually led to some of the sites shutting down operations and doing manual control for the sort – a huge operational issue even for a global company.
The Solution: 24/7 On-Call Support Across the US & Europe
E Tech Group engineers with Wonderware/AVEVA system experience were contracted to support operations, troubleshoot, address concerns, and complete modifications as needed.
Two of the larger European sites agreed to a 24/7 Emergency SCADA support contract, this soon expanded to include another twelve locations. Today there are a total of 17 European-based sites that have a 24/7 Emergency Support contract with E Tech Group.
The Results: Training Offers Client Self-Sufficiency with New Systems
E Tech Group developed and trained client team members, allowing them to create an internal support group, freeing them to be self-sufficient in maintaining the system we created. And we will continue to be there as a first call when the problems, and their solutions, seem foreign.
Contact Us
"*" indicates required fields
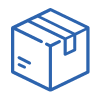
Remedying Delays & Downtime for Global Leader in Logistics
A global courier was facing delays and fines caused by an aging system. E Tech Group performed a complete overhaul of the operational infrastructure and added on-call support, eliminating all delays post-implementation.
The Project: Perform a Complete Retrofit that Eliminates Errors
A global leader in logistics and courier services located at an airport hub was experiencing routine equipment failure as their SCADA environment would freeze, crash, stall, and disrupt operations on a nightly basis. In some situations, the IT team had to restart the server environment to get the system to function.
They and the airport sort packages overnight between 11pm – 5am. So as soon as the planes land, the packages need to be taken off the plane, trucked to the facility, sorted, and placed back on another plane. All this needed to be completed before 5am so that planes could take off before 6am. If the planes didn’t take off before then, it would disrupt commercial operations and they would be fined $100k per plane.
The old system causing delays combined with the large number of packages during peak season would routinely push them past that 6am deadline, resulting in hefty fines. They were hemorrhaging time, money and reputation by the day.
The Solution: Restructure, Update & Support an Aging System
Our team of automation integrators determined an overhaul of their operational infrastructure, and the addition of on-call support would be the best solution.
E Tech Group upgraded the server environment and the software, corrected major programming errors, and supported the SCADA environment. These combined solutions eliminated the delays and fines. Due to the large scale and volume of the facility, E Tech Group worked in tandem with the client to provide continued support around managing the servers, operation updates, and providing 24/7 on-call support.
The Results: Exactly Zero Delays Experienced Post-Implementation
Since implementing the 24/7 on-call emergency SCADA support, the client has never been delayed.
The client was so pleased with the success of this upgrade and support contract that they have asked E Tech Group to tailor and scale this custom process automation solution across multiple US and European sites.
Contact Us
"*" indicates required fields
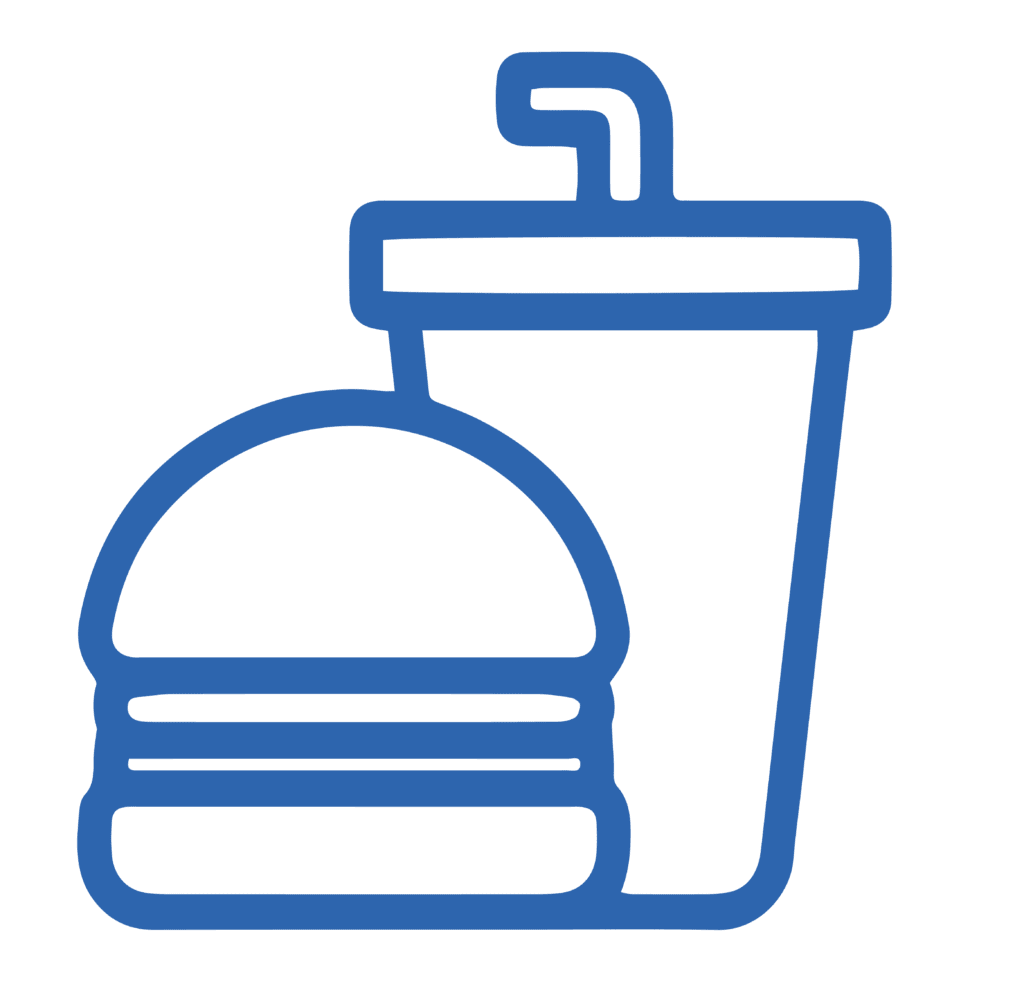
Utilizing Ignition Platform to Provide Organization-Wide Access to Quality Data
E Tech Group helped Prima Frutta increase productivity by 50% without hiring extra personnel by using the Ignition platform, which allowed remote operation of the production line and real-time data access from any smart device.
The Project: Ignite Increased Productivity with the Right Automation Platform
Manufacturers are facing costly workforce challenges. Between the labor shortage and the costs associated with employee turnover, companies are finding it difficult to increase productivity on their current automation system designs.
Prima Frutta, a cherry packaging facility in Linden, California, was struggling to maintain its production levels, but did not have the scope to add a lot of extra personnel to reach those levels. E Tech Group was called to help overhaul their control system, and under a tight timeline.
The Solution: Divide & Conquer Material Handling Automation
This control system upgrade was divided into three phases:
- Phase One: Project Planning and Documentation
- In the project’s first phase, the E Tech Group and Prima Frutta teams collaborated on planning, budgeting and documentation. They used CSIA methodologies and standards, created a detailed budget, and documented all OEM hardware into schematics that were approved before proceeding to Phase 2. This ensured the project remained on track and within budget.
- Phase Two: Wireless Network Set-Up
- The E Tech Group team successfully established a wireless network, which enabled ten tablets to remotely operate the production line through the Ignition industrial application platform from Inductive Automation. Ignition was chosen because of its flexibility, affordability and fast setup. The applications can be entirely customized quickly and easily, and data can be accessed from any smart device, including tablets, desktops, or any other smart device to allow real-time data access from anywhere the user is located.
In this project, the tablets enabled a change in process flow from anywhere in the plant, providing full SCADA control, unlike a static location. The installation process of Ignition on the tablets was seamless and took less than two hours. The Ignition software also ran on more than 120 screens throughout the plant, providing real-time data and color-coded information to employees for quick and efficient reactions.
- Phase Three: Development, Testing and Implementation
- E Tech Group used Prima Frutta’s existing server to develop modular software and PLC codes, allowing for quick deployment through component, template and user-defined type reuse.
The Result: Reaping the Fruits of a Well-Designed, Fully-Integrated Control System
The project resulted in a 50% increase in production with no additional personnel, helping Prima Frutta become the world’s largest cherry production line. The Ignition platform reduced downtime and enabled the facility to respond to changing conditions.
Contact Us
"*" indicates required fields