A PLC-5 to ControlLogix conversion within 48 hours helped improve control and visibility for a food manufacturer’s conveyor system.
Challenge
Challenges arise when hardware and software become outdated. This was the case for a leading food manufacturer who needed modernized controls for their warehouse conveyor system. The existing Allen-Bradley PLC-5 hardware was obsolete and lacked modern communication protocol. The conveyor system also lacked HMIs to monitor processes, identify problems, and visualize data. Because of this, the customer sought the help of E Tech Group, an E Tech Group company, to upgrade their Allen-Bradley PLC-5 to the latest Rockwell Automation ControlLogix processor, integrate AVEVA InTouch HMI stations, and connect devices over an EtherNet/IP communication network.
Solution
E Tech Group was challenged to migrate the PLC system within 48 hours of planned downtime. E Tech Group worked closely with the customer to understand their existing system in detail and identified potential challenges that could occur before the PLC conversion. After this step was completed, E Tech Group proceeded with the Allen-Bradley PLC-5 to ControlLogix migration, overseeing the installation and testing. E Tech Group converted the existing PLC-5 logic to its Logix equivalent and connected the new ControlLogix processor to distributed, remote, and POINT I/O racks via EtherNet/IP communication network. Then the project team configured and connected devices with AVEVA InTouch HMI to provide conveyor line operators with better visualization capabilities.
Results
This upgrade provided the food manufacturer and its operators with greater control and visibility over their conveyor system, enabling efficient fault detection, improved PLC and HMI communication, data acquisition, and technical support from the manufacturer. With this migration project completed, the customer minimized their risk of downtime, enhanced conveyor performance, and strengthened their network communications.
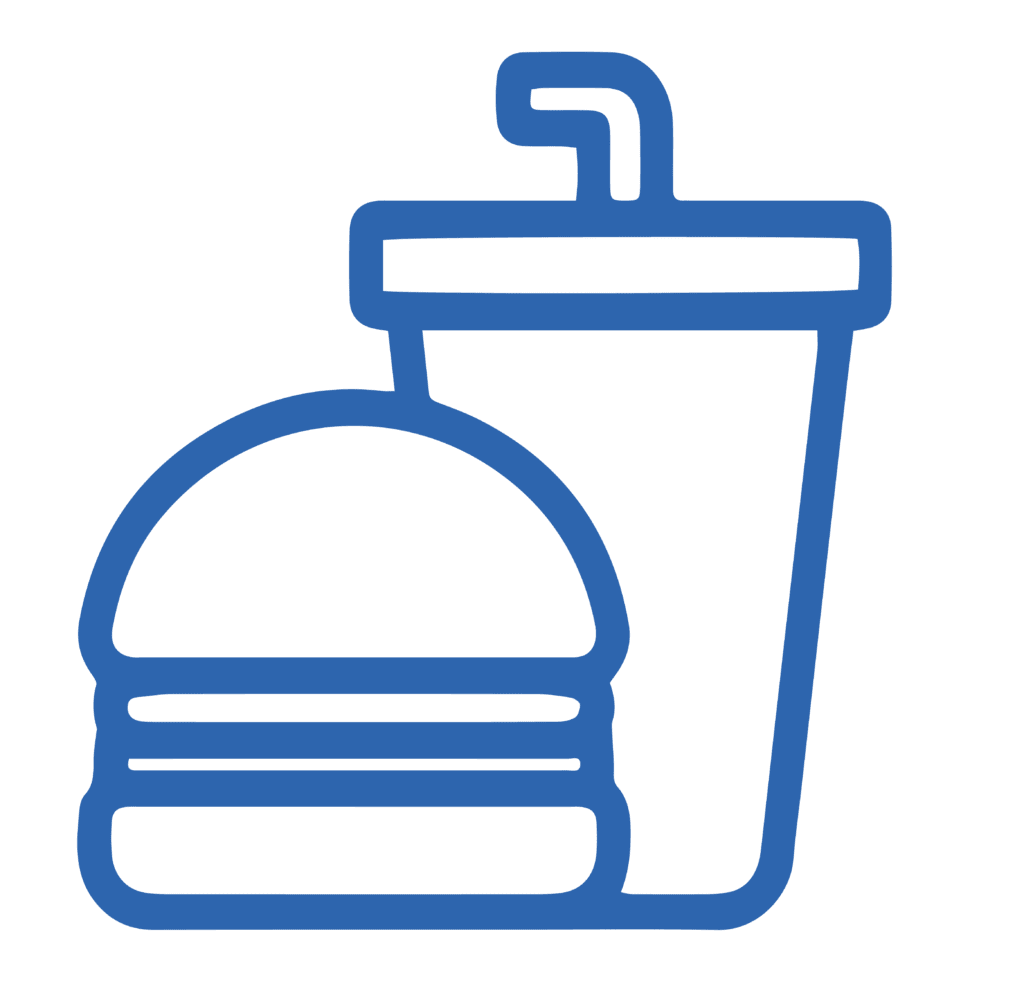
PLC-5 to ControlLogix Migration Supports Greater Uptime for Global Spice Supplier
A global supplier of spice ingredients needed to upgrade their Allen Bradley PLC-5 system. E Tech Group was recruited to modernize their obsolete PLC system to a more IIOT-friendly platform.
The Project: Remove Production Constraints with Complete Control System Upgrade
A global supplier of spice ingredients needed to upgrade their 25-year-old Allen Bradley PLC-5 system. The outdated platform was experiencing constraints and was limiting network connections. The client was seeking a system integrator that could provide timely PLC migration support using the latest technology available.
Automation Group, an E Tech Group Company was recruited to modernize their obsolete PLC system to a more IIOT-friendly platform. Automation Group, E Tech Group’s most recent acquisition, is a leading provider of automation services. They’ve worked with over 1000 clients across North America, implementing advanced control system solutions tailored to each facility’s unique challenges.
The Solution: Implement an Integrated, IIoT-Compatible Control System
E Tech Group automation professionals reverse-engineered the customer’s legacy system and analyzed existing diagrams to identify potential risks to obtain detailed information on device and wiring configurations. This step was crucial to improve control system performance and understand their control environment before moving to the design phase.
As a leading Rockwell Automation system integrator and CSIA-certified automation company, we developed a simplified migration plan using the latest technologies. We converted all networks to Ethernet/IP communications, upgraded the client’s PLC-5 system to ControlLogix and consolidated FactoryTalk View SE screens, making it easier for plant personnel to operate the system.
The Results: The First Step in a Digital Transformation
The global spice supplier’s upgrade from PLC-5 to ControlLogix was completed on schedule and improved performance, greater uptime, and a more user-friendly interface for the client’s PLC system. This upgrade project was a crucial step in the client’s digital transformation journey.
Our recent addition, Automation Group, an E Tech Group Company, designed and implemented this creative automation system solution. For more information on this control system upgrade, visit their website to read the complete case study.
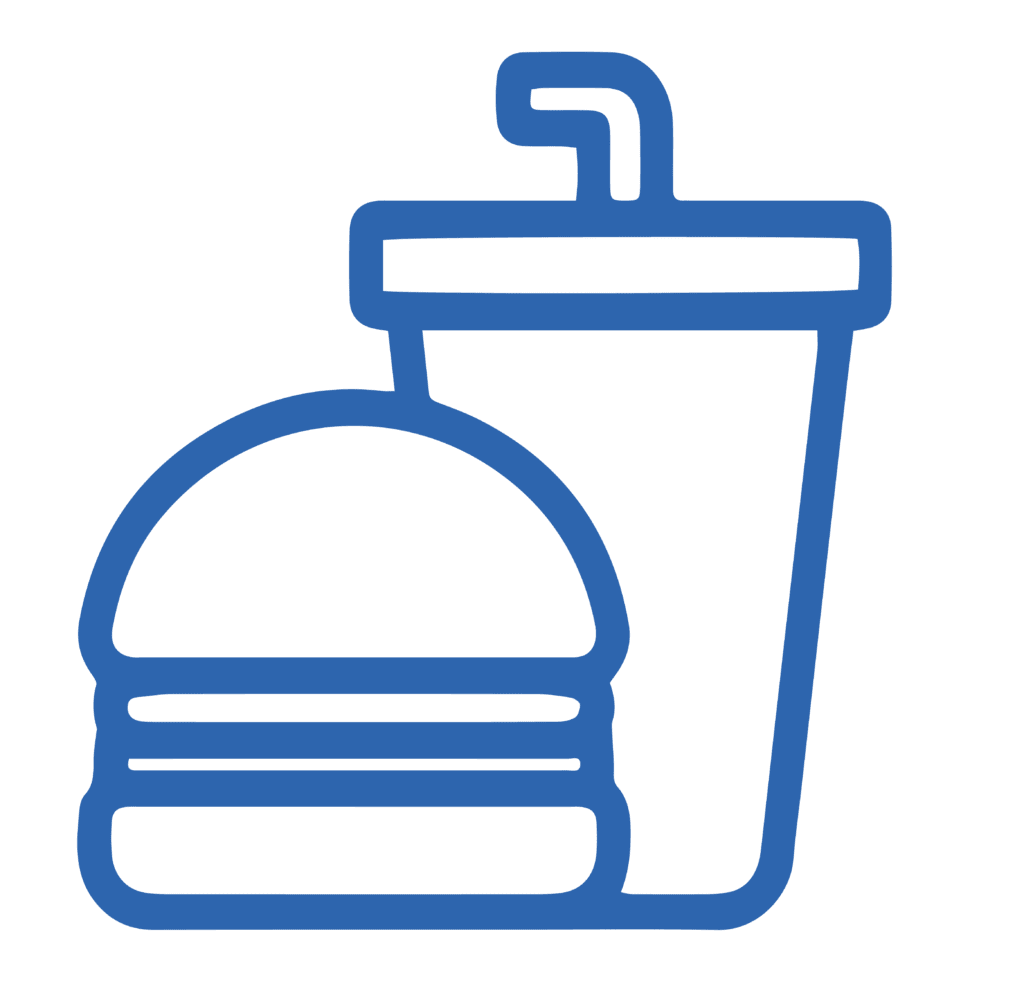
Major SCADA & PLC Upgrade Increases Uptime, Lowers Maintenance Costs for Rice Milling Company
A rice milling company needed a new PLC in a truncated timeline. Automation Group, an E Tech Group Company’s team inventoried equipment and upgraded the facility’s automation system to Ignition SCADA software, setting the client up to meet goals and be prepared for growth.
The Project: Upgrade a Facility’s Control System in 2 Days with No Downtime
A rice milling company was facing operational constraints of a legacy SCADA system. The system was costly to maintain, and the control system design caused frequent communication problems between different production areas.
The client needed a new PLC program to be installed within a 48-hour timeframe to minimize production impacts, and the existing SCADA system needed to remain operational during the migration to Inductive Automation’s Ignition platform.
The client contracted Automation Group, an E Tech Group Company as their choice system integrator given their advanced expertise in system migration and the successful execution of projects at the client’s other facilities.
The Challenge: Tread Softly with Time & Operation Constraints
There were a few obstacles to this control system upgrade that required one of the unique proficiencies of E Tech Group’s brand of automation system integration:
- An obsolete PLC controlled their rice finishing line.
- An obsolete SCADA automation application controlled the entire facility.
- The client had a strict 48-hour timeline to the upgrade implementation.
- The new SCADA needed to be implemented without disrupting the existing one.
- The new SCADA needed to be able to work alongside the legacy control system.
E Tech Group’s team knew this diverse set of obstacles would affect the course of the project, end-to-end. Our control system integrators had to find a creative way to work quickly without sacrificing our detailed approach or the quality of the upgraded automation system.
The Solution: Modular Migration Solves Everything
The project team created a site inventory of the customer’s existing PLCs, network, computers, and applications. The project included upgrades to servers, computers, and network switches in collaboration with the customer’s IT department, the upgrade to Ignition SCADA software across six applications with approximately 500 screens, and the upgrade to two ControlLogix PLC chassis.
The SCADA upgrade was completed in several phases and each application was upgraded individually. This helped minimize impacts on the customer’s production efforts and enabled the legacy and new SCADA applications to run simultaneously so the customer’s personnel could learn the new SCADA software.
The Results: Short-Term Success for Long-Term Growth
This approach to updating the facility’s control system allowed the client to improve operations and network communications at once while giving their operators time to learn the new system before getting rid of the old. Automation Group, an E Tech Group Company leverages this distinct diverse, multidisciplinary engineering approach to create intelligent automation solutions for the customer’s long-term success and the opportunity to support their operations in the years to come.
The talented automation engineers at our most recent acquisition, Automation Group, an E Tech Group Company, managed this particularly tricky project. For more information on this system upgrade, visit their website for the complete case study.
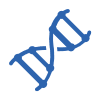
Upgrading a QBMS while Enhancing Existing Functionality
Unsupported OSs forced a client to upgrade their automation system to avoid failures. E Tech Group developed and integrated a creative solution that delivered the desired functionality between previously incompatible software and hardware components.
The Project: Update a Building-Wide Control System to Avoid Imminent Issues
A client had a QBMS (Qualified Building Management System) operating on an antiquated version of iFix and was running on an outdated OS (operating system). At a certain point, they would no longer be able to update either, preventing them from getting the most out of these systems and leaving them with an unsupported OS and HMI system.
The potential of increased downtime in the event of a failure eventually proved more costly than upgrading the entire building management system. Knowing it was only a matter of time before they would start encountering issues that could jeopardize the system’s operation and reliability, they knew it was time to work proactively.
After evaluating their options, they moved to update and upgrade the QBMS while at the same time enhancing and expanding its capabilities from monitoring building parameters (i.e. temperature, room differential pressures) and independent equipment (i.e. freezers, refrigerators, lab incubators) to monitoring production equipment and centralizing the historical data collection of all equipment at the facility.
The Challenge: Overcome Compatibility Issues & Add Functionality on a Tight Turnaround
Our team is always up for a challenge, and this project presented no shortage of them. The client was set on a PlantPAx 5.0 platform for their new QBMS. As a Rockwell Automation Gold System Integrator, our engineers have extensive experience with the Rockwell PlantPAx 5.0 building automation system, which proves a top performer in both turnkey control system builds as well as partial upgrades like this one.
But having to complete a partial upgrade in an existing system still requires a bit more analysis and research than starting from scratch. And try as you might to ensure as few potential hurdles as possible are overlooked and unrecognized once the work is underway, some can be out of your hands and unavoidable.
Our team encountered two significant challenges during the project:
1. The client selected the PlantPAx 5.0 architecture, however, some of the equipment to be displayed and monitored was not PlantPAx 5.0 based. Certain pieces of equipment didn’t even provide the data from a PLC, but instead from an OPC server which presented its own set of compatibility issues.
2. The equipment and production areas being monitored by the existing QBMS would only be able to be down for a very short time (preferably less than one working day) to perform the cutover from the old system to the new system.
It was critical to strategically plan the necessary downtime to implement the updates to their control system so we could minimize disruption to their daily operations.
The Solution: A Slow & Steady Approach Results in Methodical & Efficient Execution
To solve the non-PlantPAx 5.0 equipment problem, a PlantPAx 5.0-based PLC was set up to read the data from the equipment and the data from the OPC server was read by an OPC client which was then transmitted to the PlantPAx 5.0 PLC. This PlantPAx 5.0 PLC was then used to display the information on the HMI and from which the Historian gathered its data.
To migrate the systems from the old QBMS to the new PlantPAx 5.0 QBMS, a combined philosophy of modularity and “you can’t do everything at once” was employed. Trying to disconnect, reconnect, and validate all the I/O points from the control panels would take days.
Ultimately, the work would be done one panel at a time, one day at a time. The team converted and tested only one control system panel per day because that made the number of points being converted completed in manageable pieces, reduced the number of issues that needed to be monitored manually at one time, and limited the downtime of systems not being converted.
The Results: Immediate Improvements and Increased Compatibility
This QBMS migration was a labor of love, and the perfect example of how even partial control system upgrades can transform a facility’s operations via better industrial data management and analysis, logistical control, network communications, production quality and throughput, and more. This client now has the resources to continue enhancing their facility’s capabilities without having to face a complete rebuild.
E Tech Group supports clients with a distinct approach to control system integration, including everything from pharmaceutical automation to alternative meat production, chemicals, biologics, and more. Our creative, methodical and communicative strategy to control system design provides clients with advanced, user-friendly automation systems that prove beneficial in the present and future as they continue to grow.
Contact Us
"*" indicates required fields