Four Big Benefits of a Front-End Engineering and Design (FEED) Study
When building a new facility-wide automation system or a control system upgrade, the planning stage is perhaps the most important part; it creates the foundation for the entire project. In-depth planning can set you up for success, whereas poor planning can make the design/build process fraught with issues. You wouldn’t build a house without blueprints, a survey, or licensed contractors, right? If you start an industrial automation project (or any project) without initial evaluation and design, you could encounter a number of issues that have the potential to negatively impact the project. So, why would you begin engineering, procurement, and construction without a Front-End Engineering and Design (FEED) study? Short answer: you wouldn’t… or at least, you shouldn’t. What is a FEED Study in an Automation Engineering Project? A FEED study is designed to help produce all necessary technical documentation, validate hardware and software specifications, and accurately define the project scope. It should be performed before the design phase of the project. A FEED study typically includes: Why is a FEED Study Important in Project Planning? The FEED study is an important step in the project development process because it helps to ensure that the project (1) is feasible, (2) can be completed within budget and (3) can be delivered on schedule. These studies also help identify any potential risks to the project, which allows you to develop mitigation strategies ahead of time. There are a number of short and long-term benefits any project could see from a FEED study, most of which involve maintaining timelines and avoiding negative impacts on the projected budget. Here are the four biggest benefits: 1. Reduced Execution Costs Support Internal Funding Because projects often hinge on a shoestring budget, every penny counts when requesting internal funding. Incorrectly calculating cost has the potential to negatively impact decision … Continued
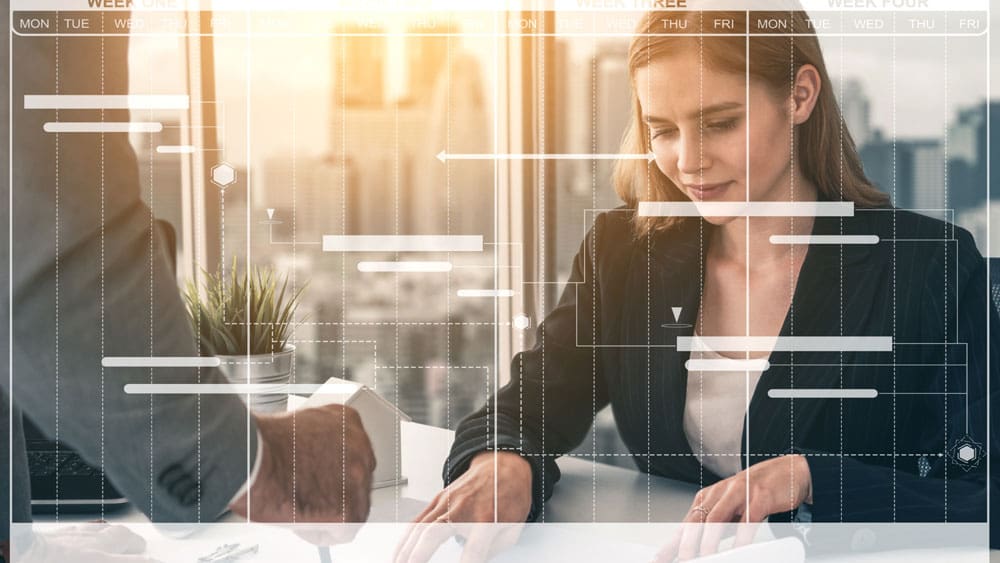