Edge series: Edge computing applications- Webcast
Applications Engineering Manager, Jeff Allen recently co-presented a webcast for Control Engineering covering how edge computing can be used for mission-critical, high-reliability automation and control applications. Applications demonstrate how edge computing can be used for mission-critical, high-reliability automation and control applications. See how system integrators have applied edge computing and see how it integrates in automation and control applications. Challenges and benefits will be discussed. Learning objectives: Understand how edge computing is being applied to automation and controls. Explore how edge computing enables certain applications. Learn how edge computing integrates with cloud resources. Review application benefits, return on investment considerations, and other benefits for automation and controls. Presented By:Jeffrey Allen, Applications Engineering Manager, E Tech GroupNate Kay, P.E., Control Systems Engineer, MartinCSI Moderated By:David Miller, Content Manager, CFE Media and Technology Click here to view the webcast.
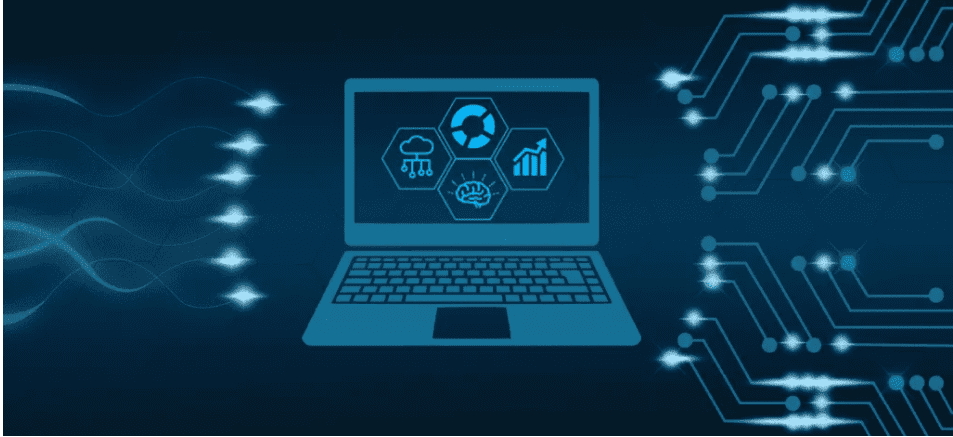