E Tech Group Names Trent Meyers, P.E. Vice President of Life Sciences Central and Process Industries
Trent Meyers, P.E. assumes the role of Vice President of Life Sciences Central and Process Industries at E Tech Group, bringing over 30 years of industry experience in management and operations. His appointment reflects E Tech’s commitment to support growth in demand for the company’s industrial engineering and automation services. West Chester, OH – April 2, 2024 – E Tech Group, a leader in providing high-quality automation, control, and engineering services for industrial clients and Gold Certified Rockwell Automation Partner, today announced hiring Trent Meyers, P.E. as the new Vice President of Life Sciences Central and Process Industries. “We are excited to welcome Trent Meyers to the E Tech leadership team. Trent has proven engineering and leadership skills with a long track record of fostering organizational growth while enhancing individual and team performance. His extensive expertise in engineering and manufacturing operations in the core industries we serve will be invaluable as we continue our growth trajectory,” said Matt Wise, CEO of E Tech Group. Meyers brings nearly 30 years of experience in engineering and manufacturing operations, including holding numerous leadership positions throughout his career. He will be responsible for leading E Tech’s Life Sciences Central and Process Industries groups encompassing consumer products, food & beverage, material handling, general industries, as well as life sciences operations. In this role, he will oversee the engineering, project management, and project delivery groups while supporting sales and marketing efforts. “Trent will be dedicated to further enhancing our client’s experience ensuring our high-quality work remains nothing short of exceptional,” said Fred Fontaine, President of E Tech Group. “His leadership will continue to drive the growth of our business by delighting current clients and attracting new ones to the E Tech family.” Prior to joining E Tech, Meyers served as Vice President of Project Delivery and … Continued
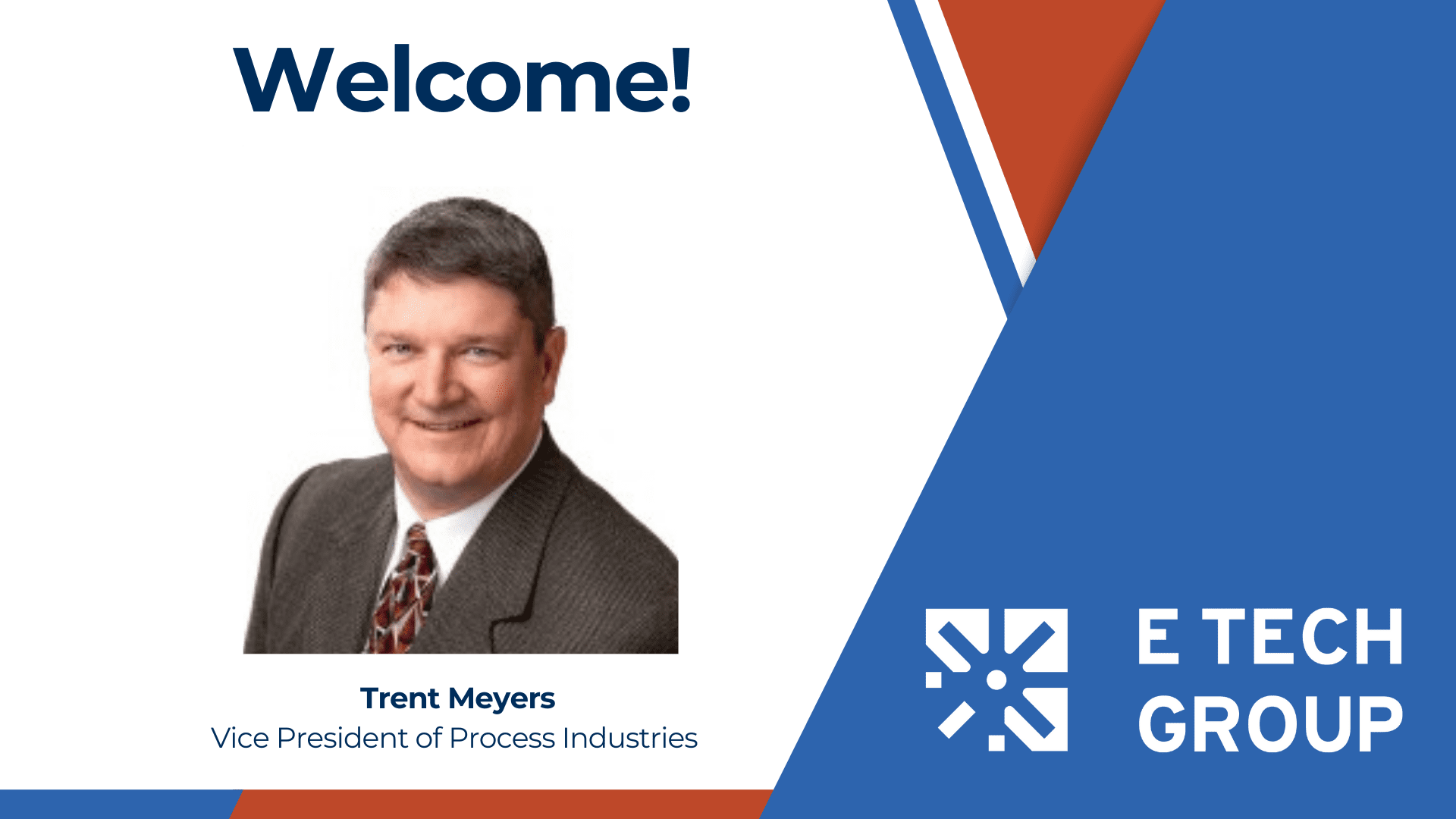