What is Digital Twin and What Does it Do?
Production line shot of digital twin palletizing line.
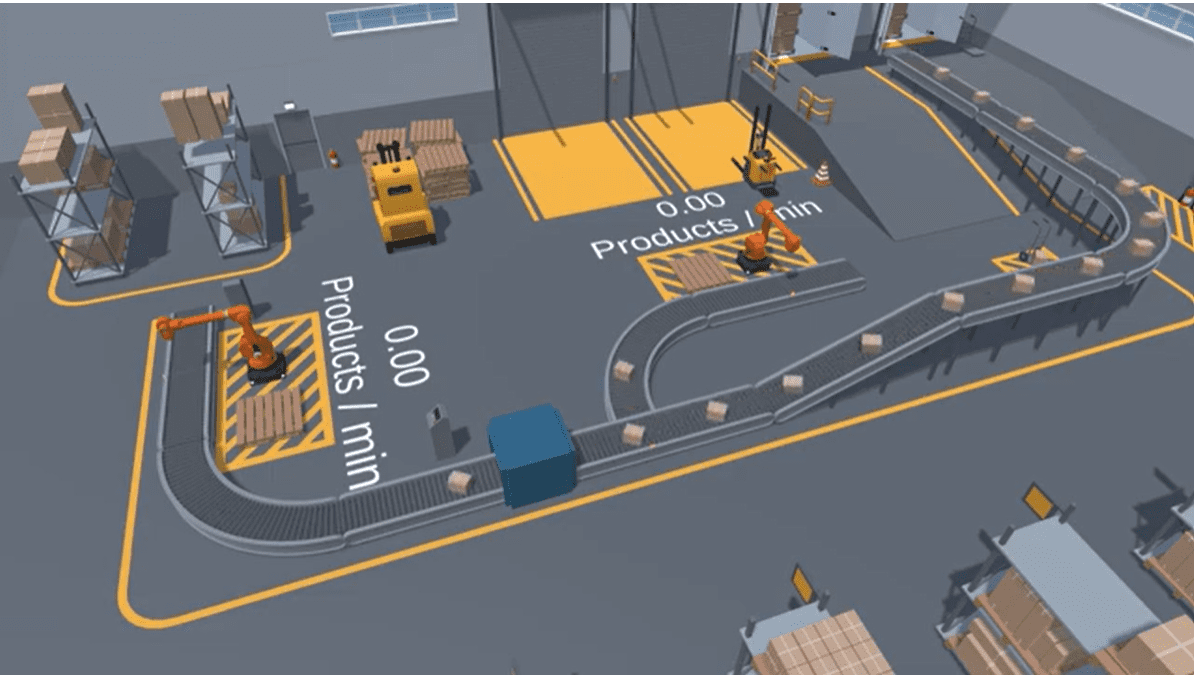
We’re your source for automation news. Keep up with the latest industry updates and E Tech employee spotlights, as well as tips and guidance from our manufacturing experts.
Production line shot of digital twin palletizing line.
In the same way you use automation to make consistent, quality products, why not use CIP to ensure germ-free cleaning every time? You’ve automated your process and packaging and have computer-generated paper trails to show food safety and quality throughout your facility. Why wouldn’t you do the same with cleaning—wherever it’s practical? Granted, there are certain pieces of equipment you just have to take out of the process to clean manually, but for other components—like piping, some conveyor belting, certain pumps, mixers, tanks and other equipment—you can clean them in place (CIP) and have automated recordkeeping to show proof of cleaning and sanitation to regulating bodies when they ask. An Expert Opinion on Sanitation Safety in Food & Beverage Automation “CIP is an integral part of cleaning and sanitation, which affects the food safety of any facility. Cleaning and sanitation not only help you comply with regulatory requirements, but also protect consumers and your brand from contamination and recalls,” says Pablo Coronel, Ph.D., CRB Senior Fellow in Food Process & Food Safety. “CIP is carried out in process lines without dismantling and must reach every nook and cranny of the process equipment; thus, well-designed equipment that is amenable to CIP (as opposed to COP—clean out of place) is a must for any installation. Materials of construction, drainability, ease of cleaning, and prevention of dead areas/zones are some of the criteria for design,” adds Coronel. Besides the equipment design, a successful CIP system depends on several variables, such as water flow rate and temperature, chemicals used (concentration) and time of cleaning. These variables are set in cooperation with the chemical supplier by the characteristics of the product to be cleaned (viscosity, stickiness, amount of fouling and presence of allergens) and the equipment that needs to be cleaned. The presence of allergens, … Continued
Taking cells from livestock to grow meat in a lab might seem like science fiction, but E Tech Group is making these processes a reality. Alternative proteins and cultivated meat are the ethical, sustainable future of meat production, and require new innovations in automation technology and control system design. Cassy Gardner, Director of Operations, and Anees Chamarty, Lead Automation Engineer at E Tech Group, Life Sciences West, discussed their work to develop a scalable and sustainable solution for cultivated meat. The first-of-its-kind pilot plant is essentially growing meat in a lab, with the help of automation. “This is something that’s not been done before, so our clients are in a very innovative space,” said Gardner. “This made early involvement with the client imperative to reducing design changes throughout the course of the project. We really had to stay, from an automation perspective, in lockstep with the clients as they evolved what they were looking to accomplish from a process perspective,” said Gardner. Utilizing Control System Software that’s Accessible but Flexible To design, program and test the distributed control system (DCS) in about six months, E Tech Group needed a platform with an out-of-the-box solution, but one that was also flexible. E Tech Group turned to Rockwell Automation’s PlantPAx platform, which is known for its robust features and adaptability. It was a time- and cost-effective solution for this control system, as it needed to be highly customizable. In addition to a tight deadline and the need for flexibility, the project included some 1,100 individual I/O points. The PlantPAx process library helped with relatively easy and quick programming, and using module programming where the state machines were embedded also helped speed things along. “So at a high level, we deliver a code that’s reusable and scalable,” said Chamarty. Batch Processing Automation: System … Continued
Adapt past the disruptors to realize benefits from industrial data analytics. Vice President of Business Development, Laurie Cavanaugh shared her insight and experience with Control Engineering for a webcast last spring in this partial transcript from the April 21, 2022, RCEP PDH webcast. Disruptors Can Slow Industrial Data Analysis Adoption The industrial data analytics course title says, “Just Enough,” but what is enough? Sometimes enough isn’t good enough because of some of disruptors to industrial automation. Back in the late ‘90s and the early aughts, it was difficult for those trying to sell computers into the industrial automation space. The user adoption just wasn’t there. People were afraid of technology. They didn’t have a computer in their home at that point, or were just getting into that. Fear of the unknown prevented full forward movement of the industrial automation space. There were generational barriers, but in just a 10-year time span from the late aughts until mid 2010s, what really disrupted that? What started changing the minds of end users in the industrial space? It was what they were doing outside of work. All of a sudden, users are starting to become a little bit bold, a little bit more creative and a little bit more demanding. Now, industrial users want the tech in every hand. They say, “I don’t understand why can’t I just go up to my human-machine interface (HMI) computer or my computer on my desk at work and key in a search and get 18 billion responses in less than one second.” Why Isn’t Machine History Available? The online shopping experience back in those days started a little bit slow, but then when people said, “Wow, I can really buy something online? Sure. I’ll give you my credit card information. I’ll tell you all sorts of … Continued
E Tech Group © 2025 | All Rights Reserved.