IIoT Grows Up, Users Ramp Up
At its root, IIoT is about getting data from sensors, instruments and other production devices to the Internet for analysis and consumption by wider circles of users—and getting analytics results back to the line. This data can be used to monitor, control and optimize automated processes, and has gained rapid traction in a variety of sectors, including: There are countless applications and benefits associated with the adoption of IIot, but the novelty has proved an obstacle in implementing these networks. What the Automation Experts are Saying About IIoT Luckily, these tasks are getting easier as users get more familiar with implementing IIoT in their processes and plant, according to Alan Maxwell, VP of the Process Industries Division at E Tech Group, an automation system integrator based in West Chester Township, Ohio and certified member of the Control System Integrators Association. “It’s getting easier for us to connect sensors and acquire signals using software like Kepware that’s part of PTC and Wonderware System Platform that’s part of Aveva, and network via OPC UA and MQTT Sparkplug protocols via Skkynet’s DataHub,” says Maxwell. “This lets them integrate third-party IoT solutions like Oden Technologies’ software for specific industries to help run analytics in cloud-based applications and improve production lines.” Stephen Veldhuis, CTO at E Tech Group, adds: “Five years ago, IIoT was a lot newer, and everyone was doing it differently. So, we evaluated the viability of IIoT and found wireless sensors and edge computing could reduce constructability time and labor, but little standardization of protocols and limited device life due to power consumption resulted in few viable cases for implementation. However, IIoT continued to evolve, mature and add new capabilities. Now, we find more workable use cases, driving adoption.” Customizing a Control System in Chicago For instance, Maxwell reports that E Tech Group’s Advanced Software … Continued
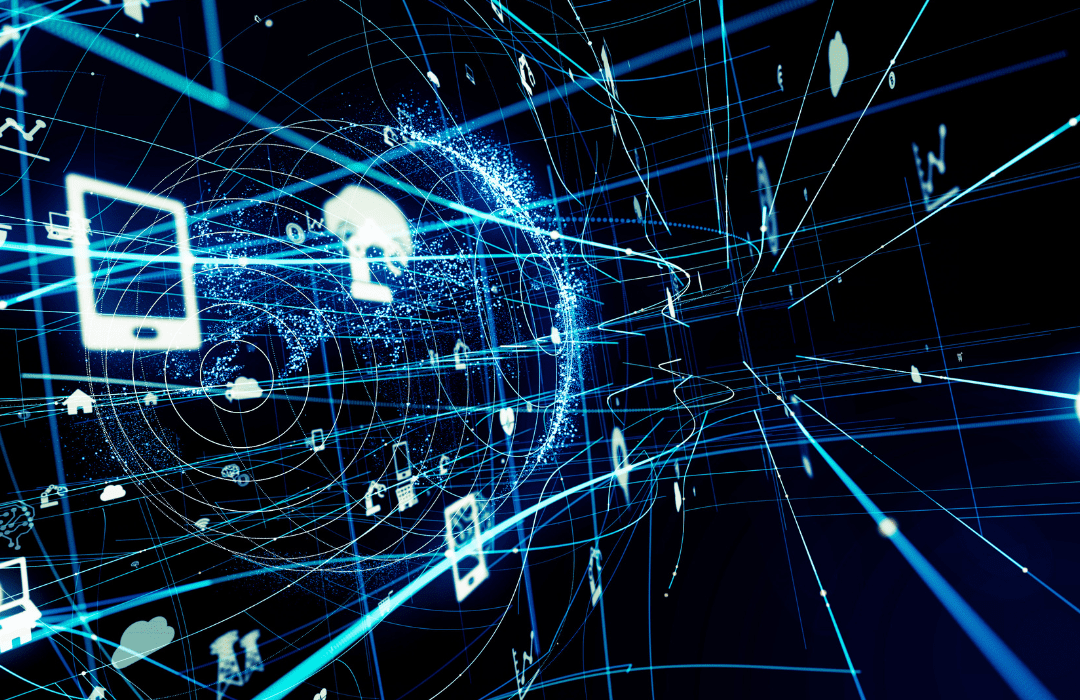