Detecting Cybersecurity Threats in Operational Technology (OT) and Industrial Control Systems (ICS)
One of the most crucial safeguards for Operation Technology (OT) is the ability to detect cyber threats within OT networks in real time. Given the importance of availability and uptime, the ability to quickly detect potential threats and respond with appropriate measures is highly stressed. Detection and prevention strategies must be carefully crafted for OT Networks to avoid excessive false positives and potentially unnecessary disruptions. Let’s look at the key characteristics of a threat detection program: Tracking key assets and data: Automatically tracking and assigning value to all OT assets, including hardware, software, and network devices. Logging and Auditing: Comprehensive logging of all activities and events for auditing and forensic analysis in a centralized system. Alerting and Response: It includes alerting mechanisms and a well-defined incident response plan to respond quickly to detected threats. Threat Intelligence: To stay informed about emerging threats specific to OT environments, the program integrates threat intelligence feeds and data from various sources. Continuous Monitoring: The program entails real-time monitoring of the OT network to detect anomalies and potential threats. Utilize your Asset Inventory to scope your Detection System Organizations need to first determine what their critical assets are and then prioritize resources accordingly, such as log retention, and frequency of log reviews making informed decisions about which log data should be forwarded to their centralized logging solution. Identify key assets and data Assess common threat vectors Review industry best practices What logs should be monitored? Not all unusual events point to malicious activity or demand further investigation. Here are some examples of events that should be monitored on a regular basis, according to the NIST 800-82r3 Publication: Information Events Account lockouts Unauthorized creation of new user accounts Unanticipated remote login activities The deliberate erasure of event logs Event logs becoming unexpectedly saturated with data Antivirus … Continued
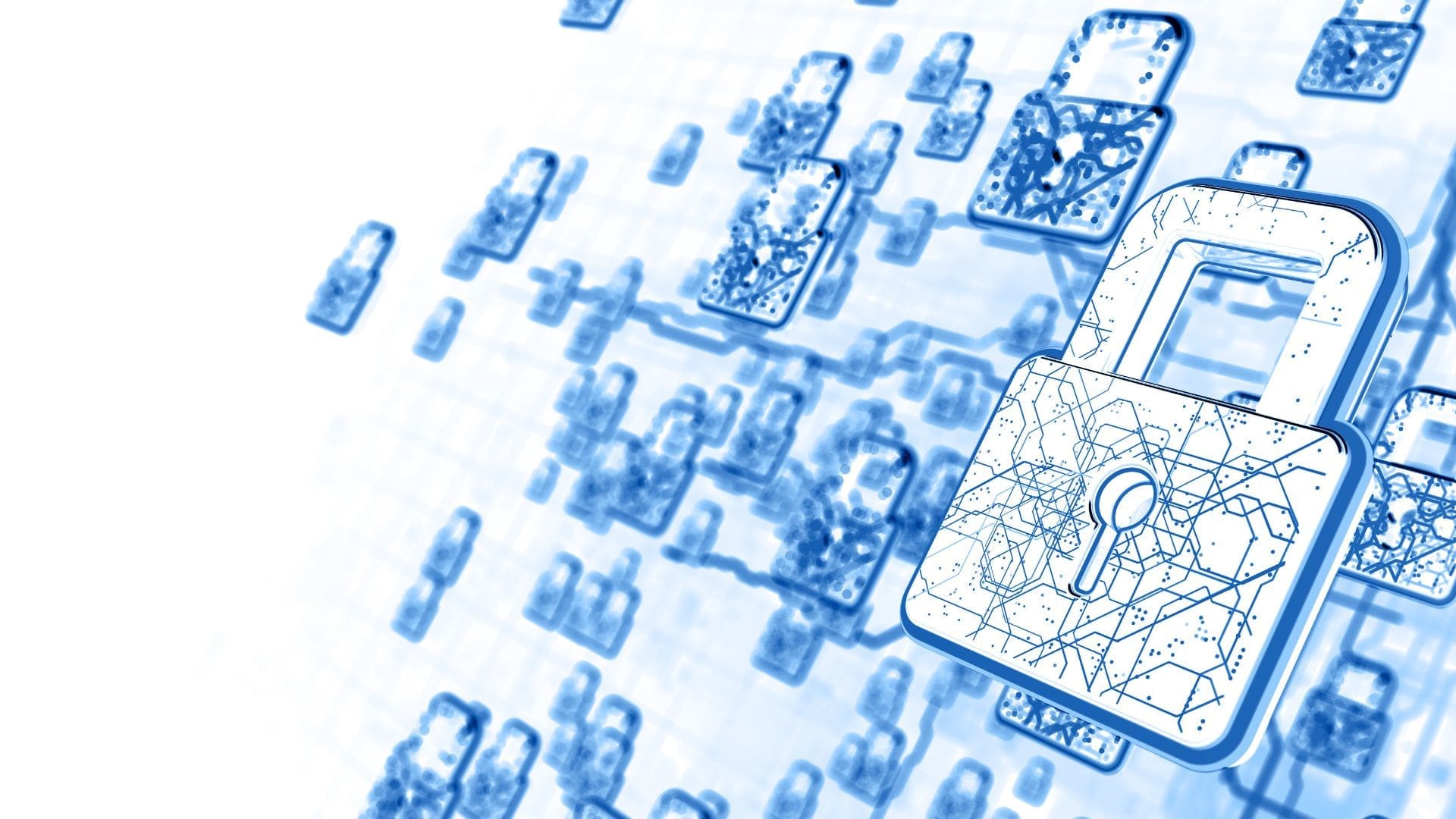