S88 Specs, Part 3 of 3: Understanding S88 States
After reviewing parts one and two of this three-part series, you now have a conceptual and visual understanding of the S88 standard and its applications. If you haven’t yet read the first two parts of this series, check out S88 Specs, Part 1 of 3: An Introduction to the S88 Standard and Part 2 of 3: System Modeling Under S88 Standard. Transitioning S88 States Throughout Production In this last entry, we’ll provide the final piece of the puzzle, bringing it all together. We’ll examine the progression through the numerous defined states associated with the manufacturing process as it aligns with S88 and the corresponding model. Understanding S88 States in Control System Modeling The S88 standard defines various states that units or phases can transition through during their operation. These states, categorized as an Initial State, and Quiescent, Final or Transient states, provide a standardized framework for interaction between recipe phases and control system equipment and control module phases. Let’s explore some of the key states defined by the S88 standard: Quiescent states Held Paused Final States Aborted Stopped Complete Initial State Idle Transient states Starting Restarting Running Aborting Holding Pausing The states listed here are the typical implementation. The procedural state model can be expanded or collapsed as permitted by the standard. The figure below shows the basic state diagram. Fig.4 State Transition Diagram SC Denotes State Change – state logic completes normally and the state advances as indicated by arrows. Text over the arrow Start, Resume etc. are external commands from batch application or internal to the control system or operator issued. The Hold, Stop, Abort are unique in that they act on multiple steps contained within the shaded rectangles. Handshake signals are implemented between the control system and batch system through command and status bits. They … Continued
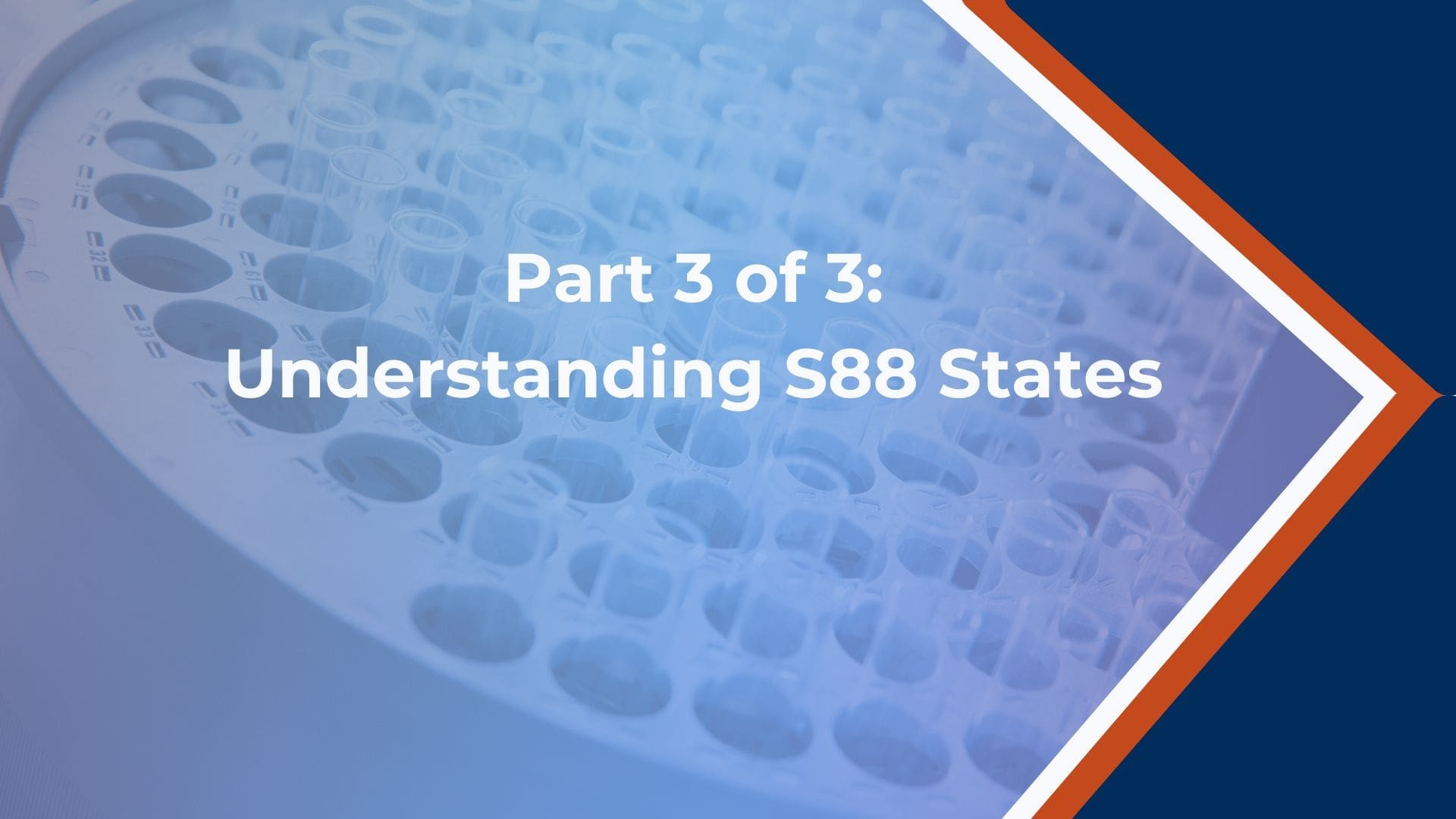